
Beschichten mit Diodenlasern
Das Beschichten mit Lasern, auch Laserauftragschweißen oder Laser Cladding genannt, hat bereits eine lange Tradition. Und die Bedeutung der Anwendung nimmt dank ständiger Material- und Technikinnovationen bis heute immer weiter zu. In den vergangenen zwei Jahrzehnten ist das Beschichten mit Lasern daher zu einer der bedeutendsten Applikation für Diodenlaser geworden. Grund genug sich das Verfahren im Rahmen unserer kleinen Serie „Diodenlaser in ihrer Anwendung“ einmal genauer anzuschauen.
Teil 3: Das Beschichtungsverfahren
Beim Laser Beschichten erzeugt der Laserstrahl auf der Oberfläche des Werkstücks ein Schmelzbad, dem zugleich ein Beschichtungsmaterial (in Pulverform oder als Draht) zugeführt und vom Laser zeitgleich mit aufgeschmolzen wird. Das Prozessergebnis ist eine zusätzliche Schicht auf der Bauteiloberfläche, die metallurgisch mit dem Grundmaterial verbunden ist.
Die Vorteile
Die metallurgische Anbindung ist weit stabiler als zum Beispiel die mechanische Verklammerung, die beim Thermischen Spritzen erzeugt wird. Kurze Einwirkzeiten und niedrige Einwirktiefen verursachen nur sehr geringen Verzug. Die Abkühlung vollzieht sich schnell. Absoluter Pluspunkt ist die homogene Intensitätsverteilung im Diodenlaserstrahl (Top-Hat-Profil): Das Strahlprofil des Diodenlasers erzeugt während des Schweißprozesses ein sehr gleichmäßiges Schmelzbad, das wiederum eine poren- und rissfreie Oberflächenbeschichtung hervorbringt. Aufgrund der hohen Oberflächenqualität sind Nachbearbeitungen so kaum erforderlich.
Mittels einer Laser Beschichtung veredelte Bauteile lassen sich heutzutage fast überall finden: Sie kommen unter anderem in der Schwerindustrie, der Fahrzeugproduktion oder der Landwirtschaft zum Einsatz. Dieses breite Einsatzspektrum ergibt sich aus der hohen Flexibilität der Laser-Technologie. Die Motivation für das Aufbringen eines Zusatzwerkstoffs kann dabei sehr unterschiedlich sein. Ein Verschleißschutz kann mithilfe des Diodenlasers ebenso zuverlässig realisiert werden, wie eine korrosionshemmende Schicht oder die Reparatur eines verschlissenen Bauteils. Je nach Anwendung sind Prozessvariationen möglich, die insbesondere die Wahl des Schichtmaterials beeinflussen.
Motivation Korrosionsschutz
Mit Laserbeschichtungen kann sowohl die Kriechkorrosion als auch die Spaltkorrosion verhindert werden. Hier werden oft Edelstähle oder Nickellegierungen auf niedrig legierte Stähle aufgebracht. Die Durchmischung der Werkstoffe liegt bei der Verwendung von Diodenlasern als Energiequelle typischerweise unter 5 Prozent. Damit reicht eine einzige ca. 1 mm starke Beschichtung bereits für einen guten Korrosionsschutz aus. Herkömmliche Verfahren erfordern in der Regel zwei Schichten und schneiden in Taktzeit und Materialeinsatz deutlich schlechter ab.
Motivation Verschleißschutz
Hier steht das Laserauftragschweißen in direkter Konkurrenz zu anderen Verfahren wie beispielsweise dem Thermischen Spritzen. Durch die metallurgische Verbindung von Zusatzschicht und Basiswerkstoff werden jedoch sehr viel längere Standzeiten erzielt. Die Realisierung eines Verschleißschutzes setzt Beschichtungswerkstoffe voraus, in denen Hartstoffe enthalten sind. Die Materialien sind häufig Ni-Basis Legierungen (In 625) mit Wolfram Karbiden. Diese können bis zu 60 Gewichtsprozent der aufgebrachten Schicht betragen.
Die Reparatur von Bauteilen
Auch das sogenannte Reparaturschweißen wird als Draht- oder Pulverauftragschweißen realisiert. Nach Abtrag der alten Beschichtungen und Reinigung der Werkstückoberfläche lassen sich dabei äußerst stabile Neubeschichtungen realisieren. Im Unterschied zum Verschleiß- oder Korrosionsschutz werden hier in der Regel identische Materialien zum Grundwerkstoff aufgebracht. So lassen sich verschlissene Oberflächen, herausgebrochene Stücke oder andere Schäden effektiv reparieren. Solange der Werkstoff schweißbar ist, sind solche Reparaturen ohne weiteres möglich – und besonders bei hochwertigen und teuren Bauteilen häufig wirtschaftlich sinnvoller als eine Neuanschaffung.
Die generative Fertigung
Der letzte besondere Bereich des Laserauftragschweißens ist das Generieren von Bauteilen, oft auch als Additive Manufacturing (AM) oder 3D-Drucken bezeichnet. Lage um Lage können dabei nach entsprechender Programmierung des Bearbeitungssystems Bauteile mit komplexen Strukturen vollständig aus Pulver oder Draht generiert werden. Neben Edelstählen kommen hier auch vermehrt Aluminium, Titan und Superlegierungen zum Einsatz, die im modernen Flugzeugbau in Turbinen, Rumpf und Flügeln verwendet werden.
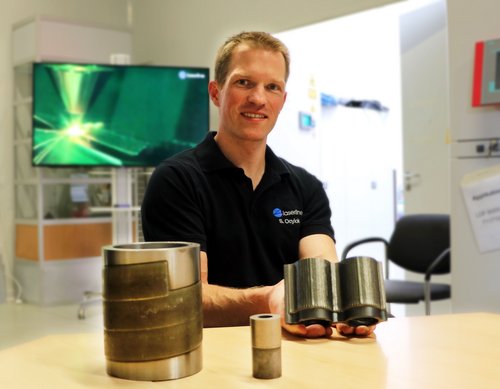
Zusammenfassung
Schon diese kurze Ausführung zeigt: Diodenlaser sind ein ideales Beschichtungswerkzeug. Nicht zufällig konnte sich das diodenlaserbasierte Auftragsschweißen in Korrosions- und Verschleißschutz sowie bei Reparaturarbeiten erfolgreich etablieren – und es gewinnt ständig weitere Marktanteile hinzu. Zusätzlich führt die kontinuierliche Entwicklung weiterer Laser Cladding-Verfahren zu einer Erschließung immer neuer Einsatzgebiete. Die Zeit des modernen Laserauftragschweißens hat gerade erst begonnen.
Erfahren Sie mehr über unsere Anwendungen im Bereich Auftragschweißen.