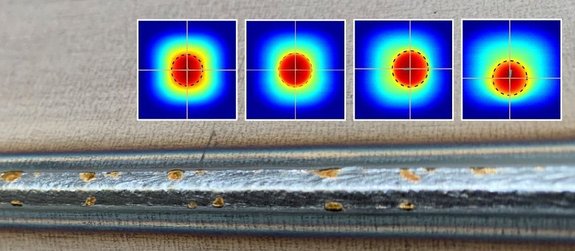
Diodenlaser verbessern Spaltüberbrückbarkeit
Die Überbrückung breiter Spaltmaße ist eine klassische Herausforderung des Metallschweißens. Im Karosseriebau stellt sie sich ebenso wie im Maschinen-, Rohrleitungs- oder Schiffbau.
Laserfügen mit Multi-Spot-Modul statt MSG-Schweißen
Bevorzugter Lösungsansatz war lange das Metallschutzgasschweißen (MSG-Schweißen) – eine klassische Fügetechnologie, die zum Aufschmelzen der Werkstücke einen elektrischen Lichtbogen nutzt. Diese Schweißlösung ist kostengünstig in der Anschaffung und hat sich zur Überbrückung breiter Spaltmaße durchaus bewährt, es gibt jedoch Schwachpunkte bei Nahtoptik und Prozesseffizienz: Neben vergleichsweise langsamen Vorschubgeschwindigkeiten haben Anwender aufgrund des hohen Wärmeeintrags mit einem beträchtlichen Verzug zu kämpfen, der teilweise aufwendiges Richten erfordert. Hinzu kommen kostenintensive Nachbearbeitungen zur Ausbesserung von Unregelmäßigkeiten.
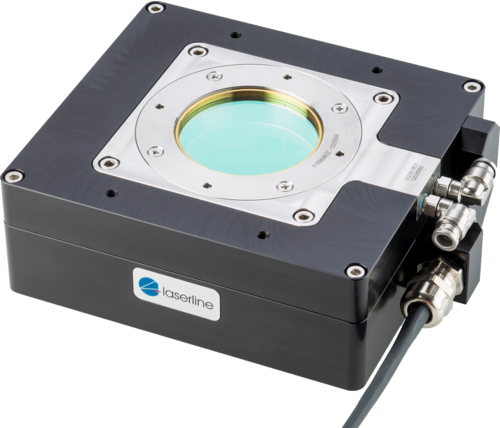
Neue Bearbeitungsoptionen beim Fügen symmetrischer und asymmetrischer Nähte
Insgesamt deutlich effektiver kann die Fügeaufgabe durch diodenlaserbasiertes Kaltdrahtschweißen mit Multi-Spot-Optiken von Laserline realisiert werden. Hierzu teilt ein Multi-Spot-Modul den kollimierten Laserstrahl auf und erzeugt auf diese Weise einen kleineren Innenspot, der von einem größeren, rechteckigen Außenspot überlagert wird. Im Schweißprozess schmilzt der Innenspot die Fugen der Werkstücke und den zugeführten Kaltdraht auf, der als zusätzliches Füllmaterial für die Naht dient – der breite Außenspot verbessert die Spaltüberbrückbarkeit, erzielt eine reduzierte Dynamik des Schmelzbades mit verminderter Spritzerbildung und glättet die Nahtoberfläche. Im Vergleich zum reinen Laserstrahlschweißen können mittels Multi-Spot-Optik und Kaltdraht dadurch Spaltmaße von bis zu einem Millimeter statt üblicherweise nur 0,1 bis 0,3 Millimeter überbrückt werden. Ergebnis des Schweißprozesses sind glatte Nähte ohne Randkerben, die keine Nachbearbeitung mehr erfordern. Durch die gezielte Anpassung von Spotgröße und Leistungsverteilung kann außerdem der Nahtquerschnitt optimiert werden. Interessante Bearbeitungsmöglichkeiten eröffnet die Spot-in-Spot-Konfiguration als Variante der Multi-Spot-Technologie insbesondere beim Fügen asymmetrischer Nähte: Der Außenspot lässt sich stufenlos verschieben und ermöglicht somit bei laufendem Prozess eine dynamische Anpassung an wechselnde Nahtgeometrien. Dadurch wird ein einseitiges Abschmelzen bei unterschiedlichen Blechdicken unterstützt, wie es beispielsweise bei Tailored Blanks gefordert wird.
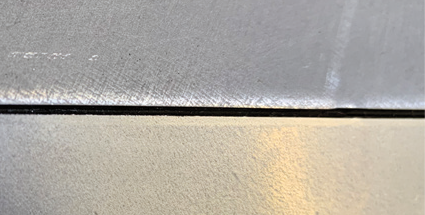
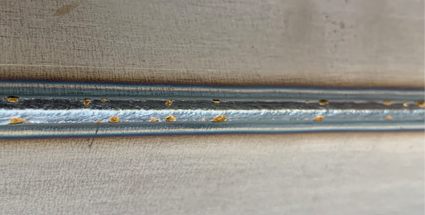
Prozessvideo: Laserfügen mit Spot-in-Spot-Design
Durch Einsatz einer Bearbeitungsoptik mit Laserline Multi-Spot Modul und Kaltdraht, können Spaltmaße von bis zu einem Millimeter überbrückt werden.
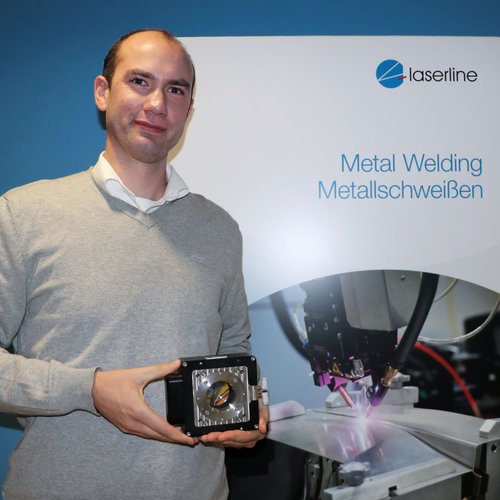
Hohe Prozessgeschwindigkeiten, kaum Verzug
Mit dem Spot-in-Spot-Design lassen sich die gewünschten Nähte außerdem deutlich schneller realisieren: Laserleistungen im Multi-Kilowatt-Bereich ermöglichen eine Verdreifachung der Prozessgeschwindigkeit im Vergleich zum MSG-Schweißen und sorgen auf diese Weise für einen höheren Output in der industriellen Serienfertigung. Zudem wird durch die gesteigerte Vorschubgeschwindigkeit der Wärmeeintrag in das Werkstück reduziert und Materialverzug dadurch effektiv unterbunden. Insgesamt sind Lasersysteme mit Spot-in-Spot-Fokus von Laserline somit eine Alternative zum MSG-Schweißen, die hinsichtlich Nahtqualität, Geschwindigkeit und Wirtschaftlichkeit nicht nur bessere Ergebnisse erzielt, sondern darüber hinaus auch neue Bearbeitungsoptionen beim Fügen symmetrischer und asymmetrischer Nähte bietet. Die Multi-Spot-Module können problemlos in Bearbeitungsoptiken eines Lasersystems der LDF-Serie von Laserline integriert werden. Bei der Wahl individueller Anwendungskonfigurationen steht der Diodenlaser-Hersteller aus Mülheim-Kärlich von der ausführlichen Beratung bis hin zu Testläufen im hauseigenen Applikationslabor gerne zur Verfügung.
Erfahren Sie mehr über das Multi-Spot-Modul!