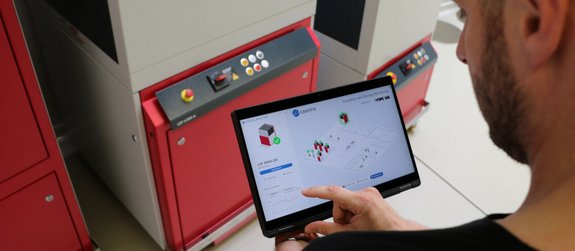
Laser 4.0 - Industrielaser in der Digitalisierung
OPC UA Schnittstellen schaffen die Voraussetzung für eine plattformunabhängige, vertikale und horizontale Datenkommunikation. Sie ermöglichen die Integration von Lasern, Lichtleitfasern und Bearbeitungsoptiken in Smart Factory Systemarchitekturen.
Der Trend zur Digitalisierung hat längst auch das Feld der Industrielaser erfasst. Laserline hat früh darauf reagiert und unter dem Stichwort Digital Laser Solutions mit der Entwicklung von Lösungen für die Integration von Lasern in digitalisierte Prozessarchitekturen begonnen. Erster Schritt: Die Ausstattung der LDF Systeme mit einer Industrie 4.0-konformen OPC UA Schnittstelle.
Laser 4.0 – keine Frage, das wird die Zukunft sein. Denn die digitale Transformation macht auch vor der Lasertechnik nicht halt. Wie sollte sie auch? Wo künftig die Smart Factory realisiert wird, wo also alle Prozessteilnehmer untereinander vernetzt sind, wo Maschinen und Geräte, Verwaltungs- und Steuerungssysteme im großen Stil miteinander kommunizieren – dort müssen auch Diodenlaser mitreden können. Die Digitalisierung einer vollautomatisierten Produktionsstraße etwa sollten auch die eingesetzten Laser mittragen. Und selbst dort, wo die Digitalisierung nicht auf Vollvernetzung hinausläuft, in kleineren mittelständischen Betrieben zum Beispiel, geht am digitalen Transformationsprozess kein Weg mehr vorbei. Ein Lohnbeschichter muss nicht Dutzende von Lasersystemen in eine vollautomatisierte Architektur einbinden – solche Strukturen aufzubauen ist für ihn nur selten sinnvoll. Die wenigen Laser, die er besitzt, wird aber auch er digital überwachen und steuern wollen. Der Grund ist derselbe wie in der Großindustrie: Weil die Digitalisierung effizientere und schnellere Prozesse verspricht, die zur Senkung von Betriebs- und Investitionskosten beitragen und ein effektiveres, konzentrierteres und angenehmeres Arbeiten ermöglichen. Industrie 4.0 wird deshalb flächendeckend kommen, sei es auf kurzem oder langem Weg.
Industrie 4.0 - Plattformunabhängige Kommunikation durch OPC UA
Wer Industrielaser baut, muss sich auf diesen Wandel einstellen, sonst wird die Zukunft anderen gehören. Laserline hat das frühzeitig erkannt und unter dem Stichwort Digital Laser Solutions mit der Entwicklung von Industrie 4.0-Lösungen für seine Diodenlaser begonnen. Die ersten Ergebnisse liegen jetzt vor: Alle Laserline LDF Diodenlasersysteme der neuesten Generation sind ab sofort auf Wunsch auch mit OPC UA Schnittstellen verfügbar. Sie beherrschen also den weit verbreiteten Kommunikationsstandard Open Platform Communications Unified Architecture (OPC UA), der einen plattformunabhängigen Datenaustausch zwischen verschiedensten Maschinen, Geräten und Steuerungssystemen ermöglicht. LDF Diodenlasersysteme können damit über die entsprechenden Schnittstellen in alle Industrie 4.0-Prozessarchitekturen auf OPC UA Basis integriert werden, was unter anderem für die großen Produktionsstraßen der Automobilindustrie und ihrer Zulieferer von elementarer Bedeutung ist. Und was noch besser ist: Laserline bietet diese Lösung auch als Retrofit für LDF Bestandssysteme an. Alle bereits ausgelieferten LDF Systeme der Generationen 5 und 6 können auch noch nachträglich mit OPC UA Schnittstellen ausgerüstet und damit für die Industrie 4.0-Integration vorbereitet werden. Die Schnittstellen werden in diesem Fall als zusätzliche Hardwarekomponenten installiert und mit der Steuereinheit des Lasersystems gekoppelt, während sie in der Werksausführung schon als Softwarebausteine in der Steuerung enthalten sind.
Für die Zukunft wird das Digital Laser Solutions Konzept natürlich nicht auf die LDF Laser beschränkt bleiben. Vielmehr soll dieser Ansatz auch auf die hochkompakten 19‘‘-Diodenlaser des Typs LDM ausgeweitet werden. Damit werden dann auch revolutionäre Systeme wie die blauen Diodenlaser der LDMblue Serie als Industrie 4.0-Ausführungen verfügbar sein. Zudem arbeitet Laserline an einfachen Handling-Anwendungen, die auch bei Einzelinstallationen von Lasern eine komfortable digitale Überwachung und Steuerung ermöglichen.
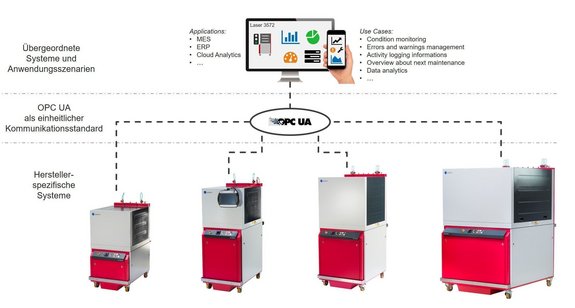
Smart Factory: Maschinendaten in übergeordneten SCADA- oder MES-Systemen
Doch was genau hat der Anwender eigentlich von der OPC UA-Fähigkeit der Lasersysteme und wie wird das damit verbundene Potenzial aktiviert? Durch die Einführung der OPC UA Schnittstelle können die Lasersysteme in umfassende Industrie 4.0-Kommunikationen eingebunden werden. Durch die Bereitstellung eines detaillierten Datenpools schaffen sie dabei die Grundlage für datenverarbeitende Folgeprozesse im produzierenden Umfeld – ist eine quantitativ und qualitativ zureichende Datenbasis doch Voraussetzung aller innovativen Analysen und Auswertungen.
Grundsätzlich braucht jede OPC UA Schnittstelle einen OPC UA Client als Gegenstück. In Industrie 4.0-Architekturen ist dieser Client gewöhnlich in ein übergeordnetes SCADA- oder MES-System oder eine Cloudlösung integriert und dient dort quasi als Schlüssel zum Schloss der Schnittstelle. Was er erschließt? Im Falle des Diodenlasers nichts anderes als die Maschinendaten. Und das sind so einige: Bei Laserline LDF Systemen, die ab Werk mit OPC UA Servern ausgestattet sind, kann der Anwender je nach Laserkonfiguration zum Teil über 300 Werte auslesen, bei Systemen mit Retrofit immerhin rund 150. Damit wird so ziemlich alles greifbar, was man über den Laser wissen möchte: Wie hoch sind aktuelle und maximale Ausgangsleistung? Wie steht es um die Temperaturentwicklung im System? Ist mit dem Kühlwasserdurchfluss alles in Ordnung? Ist womöglich Feuchtigkeit eingedrungen, die einen zeitweiligen Shutdown des Lasers erforderlich macht? Wie lautet die Seriennummer des angesteuerten Systems und wie viele seiner vorgesehenen Betriebsstunden sind bereits absolviert?
Maschinendaten
Solche und ähnliche Fragen werden durch die Maschinendaten sehr präzise beantwortet. Hinzu kommen automatische Warnhinweise und Fehlermeldungen, die auf kritische Entwicklungen aufmerksam machen. Der Anwender kann sein System also optimal überwachen und alle Systemzustände in seine Prozessplanung einbeziehen. Das reduziert die Gefahr von Prozessfehlern und verhindert insgesamt manch unliebsame Überraschung. Über solche konventionellen Datenanalysen und -diagnosen hinaus schafft die Bereitstellung von Daten via OPC UA aber auch die Grundlage für zukunftsweisende Analysen, die auf Ansätzen Künstlicher Intelligenz basieren.
Besondere Vorteile im Wartungsbereich: Condition Based Maintenance
Ganz besondere Vorteile erschließen der Datenzugriff und die damit erreichte Transparenz im Wartungsbereich. Hier wurden in der Vergangenheit, ähnlich wie im KFZ-Umfeld, periodische Wartungen vorgenommen – sei es nach Systemalter oder nach Betriebsstunden. Dieser starre Ansatz war nicht immer optimal, da jede Anwendung das System auf ihre Weise beansprucht und Fehler bevorzugt abseits der Wartungszeitpunkte auftreten. Anhand der umfangreichen Maschinendaten, die sich über die OPC UA Schnittstelle auslesen lassen, kann der Anwender demgegenüber einen weitaus flexibleren und praxisnäheren Wartungsweg beschreiten. Da alle relevanten Daten verfügbar sind, lässt sich zukünftig eine vorausschauende bzw. zustandsbedingte Wartung (Predictive bzw. Condition Based Maintenance) umsetzen. Der Laser wird also nur dann gewartet, wenn sein aktueller Zustand es erfordert – oder noch besser: schon dann, wenn sich absehen lässt, dass ein kritischer Zustand erreicht werden könnte. Man wartet also erst gar nicht darauf, dass es brenzlig wird, sondern greift frühzeitig sein. Mit diesem Ansatz können Ausfallzeiten minimiert und zudem beizeiten einkalkuliert werden, sodass ggf. Ersatzsysteme zum Einsatz kommen. Tritt doch einmal ein unerwarteter Fehler auf, ist die Suche dank des großen Datenpools meist weit schneller beendet als bisher – auch dies ein wichtiger Prozessvorteil.
Auch der eigentliche Wartungsprozess lässt sich durch diesen Ansatz optimieren. Ist der Servicedienstleister mit dem Anwender vernetzt, so ermöglicht die Datenauslesung eine automatisierte Servicekoordination: Sobald ein Wartungsbedarf erkennbar wird, erhalten die zuständigen Servicetechniker dann einen automatischen Hinweis. In einer vollvernetzten Smart Factory lässt sich dieser Prozess sogar bis zur automatisierten Terminvergabe ausbauen. Allemal aber ermöglicht er eine weitgehend reibungslose Abstimmung.
Und wenn der Laser am Ende seines Lebenszyklus ankommt? Auch das lässt sich aus den Daten ersehen, und auch hier bewährt sich die OPC UA Schnittstelle, indem die entsprechenden Warnmeldungen ihren Adressaten rechtzeitig erreichen. Dass dieser dann auch rechtzeitig reagiert und Ersatz beschafft – das kann die Schnittstelle dann leider nicht mehr sicherstellen. Der Anwender kann aber zumindest eines nicht behaupten: dass er von nichts gewusst hätte.
Interview mit Dr. Alexander Arndt, Manager Digitalization and Process Design
Ach übrigens: LDF Diodenlaser mit OPC UA Schnittstellen werden aktuell bereits erfolgreich im industriellen Umfeld als Basis für kundenspezifische Analysen der Lasersysteme eingesetzt. Das zeigt deutlich, dass der eingeschlagene Weg der richtige ist. Wie schon eingangs gesagt: Hochleistungsdiodenlaser 4.0 – das wird die Zukunft sein.
Fragen zu OPC UA oder der Integration von unseren Laserystemen in Smart Factory Systemarchitekturen?
Sprechen Sie uns gerne an!
Kontakt