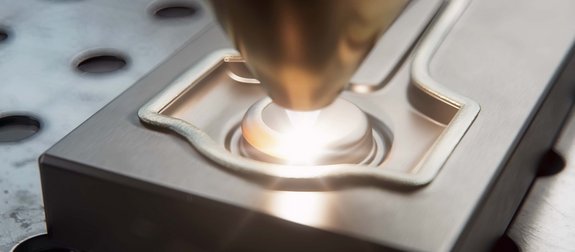
Laserauftragschweißen heute: Wo steht die Technik? (Teil III)
In der Trias der großen Einsatzgebiete des Laserauftragschweißens nimmt das sogenannte Reparaturschweißen eine Mittelstellung ein. Es weist sowohl Gemeinsamkeiten mit dem Cladding als auch mit der Additiven Fertigung auf, repräsentiert jedoch letztlich eine eigene Verfahrenswelt. Welche Reparaturen dort umgesetzt werden und wie – das verraten wir heute im dritten Teil unserer Serie über die verschiedenen Varianten des Laserauftragschweißens.
Teil 3: Reparaturbeschichten
Walzen, Zahnräder, Antriebswellen, Werkzeuge – Metallbauteile, die starken Belastungen ausgesetzt sind, weisen früher oder später fast immer Risse oder schadhafte Oberflächen auf und sind dadurch nicht mehr voll einsatzfähig. Das Ende ihrer Lebenszyklen ist deshalb aber nicht zwingend erreicht. Statt das Bauteil gegen eine Neuanschaffung auszutauschen, ist es in vielen Fällen die wirtschaftlichere und auch schnellere Lösung, eine Instandsetzung anzustreben. Das Zauberwort heißt hier Reparaturbeschichtung: Risse oder beschädigte Schutzschichten werden geschlossen bzw. erneuert, Abbruchteile wiederhergestellt, und das Bauteil erhält schlussendlich seine volle Funktionsfähigkeit zurück.
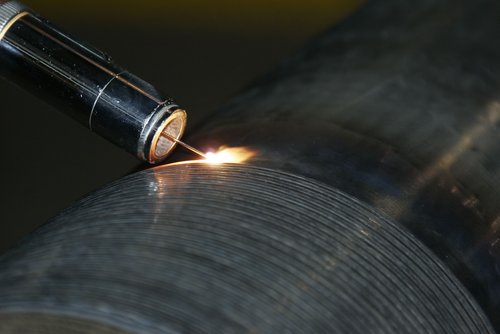
Gängige Methoden
Gängige Methoden für solche Reparaturbeschichtungen waren in der Vergangenheit konventionelle Schweißverfahren, welche meist handgeführt oder nur teilweise automatisiert sind. Bei diesen Beschichtungstechnologien wird meist unter Einsatz eines Lichtbogens ein Metalldraht oder -pulver auf der Werkstückoberfläche aufgeschmolzen und erzeugt die vorgesehene Reparatur- oder Schutzschicht. Nachteile dieser Verfahren sind der hohe Wärmeeintrag: Er verursacht nicht selten einen starken Bauteilverzug sowie eine große Aufmischung mit dem Grundwerkstoff – der Prozess ist dadurch insbesondere für filigrane Bauteile ungeeignet. Als Alternative wird deshalb immer häufiger das diodenlaserbasierte Reparaturbeschichten eingesetzt. Es kommt mit moderaten Wärmeeinträgen aus, erzeugt porenfreie Schichten und ermöglicht auch bei filigranen Bauteilen eine schnelle, effiziente und einfache Reparatur. Hierbei kann eine Bandbreite wirtschaftlicher Reparaturen kleiner einem Millimeter bis zum Großbauteil mit Reparaturen mehrerer Quadratmeter je nach Anforderung und Bauteil abgedeckt werden.
Der laserbasierte Reparaturprozess weicht im Kern nur minimal von dem des Claddings (Erstbeschichtung) ab und ist gleichermaßen zur Erneuerung schadhafter Beschichtungen wie auch zum Schließen von Rissen und zur Reparatur defekter oder fehlerhafter Formen geeignet. Bei Beschichtungsreparaturen wird zunächst das verschlissene defekte Werkstoffvolumen abgetragen, die Oberfläche des Werkstücks gereinigt und die Kontur mechanisch vorbereitet. Im Anschluss kann das Beschichtungsmaterial – Draht oder Pulver – auf das Bauteil aufgebracht werden: Hierfür wird es dem lokalen Schmelzbad auf der Werkstückoberfläche zugeführt und mit aufgeschmolzen. Im Unterschied zum Auftrag eines Verschleiß- oder Korrosionsschutzes kommen aber in der Regel mit dem Grundwerkstoff identische Materialien oder härteres Metall zum Einsatz. So entsteht eine strapazierfähige Neubeschichtung, die metallurgisch mit dem Bauteil verbunden ist. Die Dicke der aufgebrachten Schicht kann dabei je nach Anwendungsbereich variieren.
Ein typisches Beispiel für solche Reparaturbeschichtungen findet sich in der Getriebetechnik: Antriebswellen wurden hier bisher oft mit einer speziellen Verschleißschutzbeschichtung aus Keramik versehen, die jedoch auf kurz oder lang Schäden aufwies bzw. abblätterte. Diese Schäden waren früher irreparabel, was dann auch für die Welle das Ende ihrer Standzeit bedeutete. Durch das diodenlaserbasierte Reparaturschweißen hat sich diese Situation von Grund auf verändert. Nach Entfernung der alten Keramikschicht wird nunmehr mit Heizdraht aus Edelstahl eine neue Verschleißschutzbeschichtung aufgetragen. Diese Schutzschicht ist weit langlebiger als eine Keramikbeschichtung, verursacht aber nur ein Viertel der Kosten – in der Gesamtkostenbetrachtung ein ganz erheblicher Vorteil.
Weitere prominente Beispiele wirtschaftlicher Reparaturen sind Formen und Werkzeuge der Urform- und Umformtechnik, sowie Lagersitze, Kurbelwellen, Kolbenringnuten, Turbinenschaufeln und viele weitere.
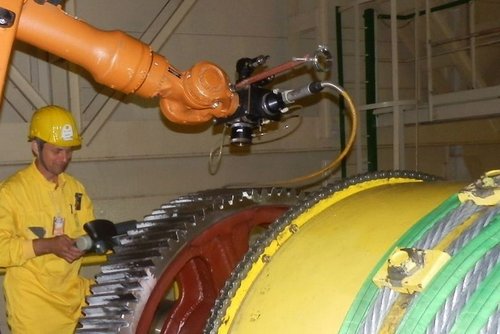
Reparatur von Rissen
Die Reparatur von Rissen oder Abbruchstellen vollzieht sich im Prinzip nach demselben Muster – nur dass hier Risse und beschädigte Konturen schichtweise aufgefüllt bzw. wieder ausgebaut werden. Dank leichter, kompakter mobiler Laser, die sich sogar für einen Einsatz auf schmalen Gerüsten in großen Höhen eignen, kann dieses Verfahren selbst an schwer zugänglichen Stellen umgesetzt werden, etwa bei fest verbauten großen Zahnrädern. In all diesen Prozessen punktet das laserbasierte Reparaturbeschichten mit einer endkonturnahen Wiederherstellung der Bauteilgeometrie, einer geringeren Wärmezufuhr und einer dementsprechend niedrigeren thermischen Belastung des Bauteils, die kaum Verzug verursacht. Auch besonders empfindliche Komponenten können dadurch problemlos bearbeitet werden. Nachbearbeitungen sind kaum erforderlich.
Fazit
Beim Reparaturschweißen auf die Diodenlasertechnologie zu setzen, zahlt sich als sowohl im Hinblick auf Effektivität und Wirtschaftlichkeit als auch unter Qualitätsaspekten aus. Die effiziente, einfache Reparatur von Beschichtungen ist ebenso möglich wie das Schließen von Rissen oder das Wiederherstellen abgebrochener Konturen. In diesem letztgenannten Punkt überschneidet sich das Reparaturbeschichten dann aber auch schon mit dem dritten großen Anwendungsbereich des Laserauftragschweißens: der Additiven Fertigung, oft als 3D-Druck bezeichnet. Diesem zukunftsweisenden Verfahren werden wir uns im vierten und letzten Teil unserer Serie widmen.
Erfahren Sie mehr über das Reparaturschweißen.