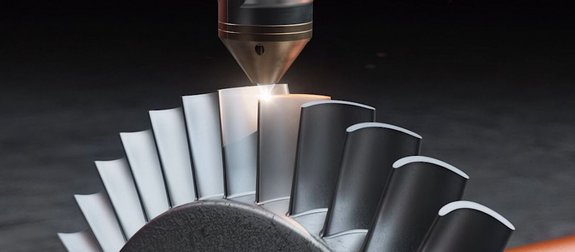
Laserauftragschweißen heute: Wo steht die Technik? (Teil IV)
Das Laserauftragschweißen ist mittlerweile in zahlreichen industriellen Fertigungsbereichen angekommen. Dazu zählt auch die Herstellung komplexer Bauteile im Schichtbauprinzip – auch bekannt als Additive Fertigung oder 3D-Druck. Diesem Anwendungsbereich widmet sich nun der letzte Teil unserer Serie.
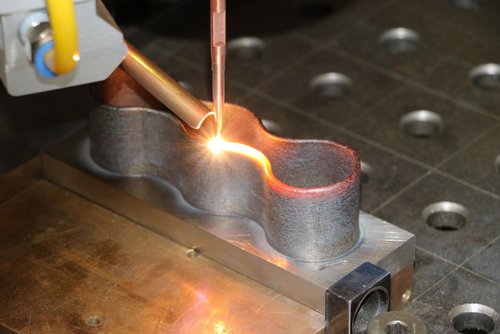
Teil 4: Additive Fertigung
Die Bedeutung der Additiven Fertigung – oft auch als 3D-Druck bezeichnet – hat in den vergangenen Jahren erheblich zugenommen, und das aus gutem Grund. Denn sowohl Umformtechniken als auch subtraktive Fertigungsmethoden, bei denen Bauteile durch zerspanende Verfahren generiert werden, sind aufgrund mangelnder Konstruktionsfreiheiten im Herstellungsprozess für die Anfertigung komplexer, individueller Bauteile nicht optimal geeignet – hinzu kommen oft erhebliche Materialverluste. Additive Fertigungsverfahren hingegen ermöglichen durch die Technologie des schichtweisen Aufbaus eine einfache Realisierung dreidimensionaler Bauteile mit komplexen Geometrien und bewähren sich insbesondere in Fällen, in denen ein hohes Maß an Individualisierung erforderlich ist. Zudem geht hier weitaus weniger Material verloren als im Verlauf eines zerspanenden Verfahrens.
Unter den konkurrierenden additiven Fertigungsverfahren hat im industriellen Umfeld zuletzt vor allem die vergleichsweise junge, lasergestützte Methode mehr und mehr an Reichweite gewonnen. Ursprünglich nur für die schnelle Erstellung eines oder mehrerer Prototypen entwickelt, dient die generative Fertigungsmethode unter Einsatz von Lasern längst auch zur Herstellung vollwertiger Formen und Kleinserien. Darüber hinaus hat das Verfahren auch in das Reparaturschweißen Einzug gehalten – sei es in der Reparatur von Abbruchstellen oder für die Wiederherstellung von Oberflächenstrukturen. Bewährt hat sich vor allem die additive Fertigung mit Diodenlasern, die am klassischen Auftragschweißen orientiert ist, wohingegen sich das LPBF-Verfahren (Laser Powder Bed Fusion) – bei dem das Bauteil durch selektives Strahlschmelzen in einem Pulverbett generiert wird – bisher noch als zu langsam und kostenaufwändig präsentiert. Größter Konkurrent aus der Gruppe der nicht-laserbasierten Verfahren ist derzeit das WAAM (Wire Arc Additive Manufacturing) – ein drahtbasierter Prozess, der zum Aufschmelzen von Schichtmaterial und Oberfläche einen elektrischen Lichtbogen nutzt. Der hohe Wärmeeintrag, der teilweise starken Verzug verursacht, sowie die geringe Endkonturgenauigkeit und unruhige Schmelzbädführung mit starker Spritzerbildung erweisen sich hier jedoch wiederholt als Nachteil.
Mag das diodenlaserbasierte Verfahren auch dem Auftragschweißen ähneln – mit dem Unterschied, dass hier dreidimensionale Formen realisiert werden –, so gestaltet sich der Verfahrensaufbau allerdings letztlich etwas anders: Gearbeitet wird mit einem System, das sich aus einem Laser, einem beweglichen 3D-Druckkopf sowie einer Metallpulverdüse oder Drahtzuführung zusammensetzt. Während des Prozesses bewegt sich der Druckkopf nach Maßgabe des dreidimensionalen Konstruktionsplans über die Bauplattform und schmilzt Werkstückoberfläche und Schichtmaterial auf. Als Schichtmaterial kommen Edelstähle, aber auch Metalle wie Aluminium und Titan sowie Superlegierungen zum Einsatz, wie sie zum Beispiel im Flugzeugbau verwendet werden. Im Zuge des Fertigungsprozesses kann darüber hinaus auch zwischen verschiedenen Materialien gewechselt werden. Somit lassen sich durch bedarfsgerechte Werkstoffauswahl unterschiedliche Anforderungen, wie Verschleißbeständigkeit, Wärmeleitfähigkeit und Duktilität in einem Bauteil vereinen, welche durch einen homogenen Werkstoff allein nicht erfüllt werden können. Nach der Erstarrung und Abkühlung des aufgebrachten Werkstoffs folgt jeweils die nächste Schicht, das Bauteil wird so Lage für Lage aufgebaut. Formen und Strukturen werden so letztlich in einem durchlaufenden Prozess realisiert – und das fast ohne Materialverlust, Nacharbeit und Werkzeugverschleiß. Das Top-Hat-Profil des Diodenlasers sorgt überdies für gleichmäßige Schmelzbäder, eine ruhige Prozessführung und homogene, rissfreie Materialschichten.
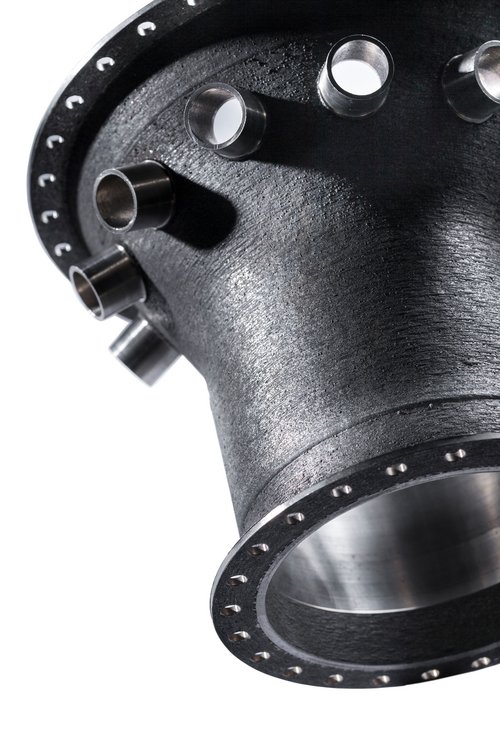
Die Vorteile
Die Vorteile gegenüber den konkurrierenden Ansätzen werden schnell deutlich: Im Vergleich zum LPBF-Verfahren werden mehr als 10fach größere Aufbauraten erzielt und somit eine deutlich kürzere Prozesszeit. Verglichen mit dem WAAM-Verfahren hingegen punktet die diodenlaserbasierte Methode durch ruhige, spritzerarme Schmelzbäder sowie einen geringeren Energieeintrag, der eine Minimierung des Bauteilverzug ermöglicht. Zur Produktionsprozessoptimierung ist zusätzlich eine Integration der Laserstrahlquelle in Werkzeugmaschinen möglich. In Fräsmaschinen etwa kann auf diese Weise ein Wechsel von additivem Pulverauftrag und subtraktivem Zerspanen realisiert werden: Der Laser ist dann für den Pulverauftrag verantwortlich, der Fräskopf für die spanende Nachbearbeitung. Beim Einsatz in zwölfachsigen Fräsmaschinen weiten sich die Anwendungsmöglichkeiten der Strahlquelle sogar noch weiter aus: Hier kann sie neben dem Pulverauftrag auch zum Schweißen und Härten eingesetzt werden – unter Zuhilfenahme entsprechender Optiken.
Fazit
Kein Wunder also, dass die laserbasierte additive Fertigung immer mehr gefragt ist: Auch Bauteile mit komplexen, individuellen Geometrien lassen sich mit geringem Materialverlust und fast ohne Nachbearbeitungen realisieren – zudem überzeugen die fertigen Werkstücke durch Rissfreiheit und insgesamt sehr hohe Materialqualität. Das Auftragschweißen mit Diodenlasern überzeugt also letzten Endes auch da, wo man es spontan vielleicht gar nicht vermuten würde. Damit sind wir dann am Ende angelangt – freilich nur am Ende unserer Serie, nicht aber am Ende des Laserauftragschweißens. Denn dessen Zukunft hat trotz aller Erfolge gerade erst begonnen.
Erfahren Sie mehr über Additive Fertigung.