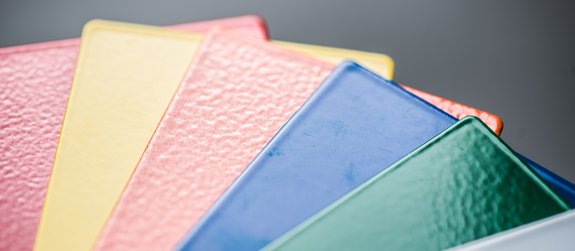
Laseraushärten von Pulverlacken
Die Laseraushärtung bietet eine präzise, energieeffiziente Alternative zu herkömmlichen Konvektionsöfen und verringert die Umweltbelastung bei Pulverbeschichtungsprozessen. Lesen Sie den vollständigen Artikel für weitere Informationen.
Ein Schritt zur grüneren und wirtschaftlicheren Produktion
Neue Einsatzgebiete für Diodenlaser sind nicht immer das Ergebnis radikaler Innovationen. Oft genug ergeben sie sich aus der Übertragung technischer Konzepte, die ursprünglich für ganz andere Anwendungen gedacht waren. Ein aktuelles Beispiel ist das Laseraushärten von Pulverlacken. Es nutzt die Ultra Wide Spot Bestrahlungstechnologie, die zum Trocknen von Batterieelektroden entwickelt wurde und macht dadurch – wie schon beim Batterietrocknen – der Wärmebehandlung im Konvektionsofen Konkurrenz.
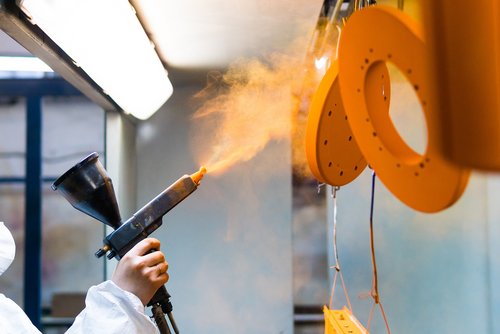
Pulverlackierungen gehören seit Jahrzehnten zu den gängigen Bauteilbeschichtungen. Sie dienen meist dem Farbauftrag oder dem Korrosionsschutz – nicht selten wird auch beides kombiniert – und kommen häufig bei planen Metallbauteilen wie Blechen, Paneelen, Lamellen oder Garagentoren zum Einsatz. Sie zeichnen sich durch hohe chemische und mechanische Widerstandsfähigkeit aus und sind insgesamt deutlich stabiler als zum Beispiel Nasslackierungen. Schwierigkeiten bereitet allerdings das Beschichtungsverfahren, das zwar technisch etabliert ist, sich in wesentlichen Teilen aber zunehmend als unwirtschaftlich und ökologisch fragwürdig erweist. In der Industrie besteht dementsprechend großes Interesse an Konzepten zur Verfahrensoptimierung. Diodenlaser, so viel zeichnet sich jetzt schon ab, könnten dabei eine wichtige Rolle spielen.
Bei Metallbauteilen werden Pulverlackierungen heute standardmäßig mithilfe von Prozessen der Elektrodynamik und der Wärmebehandlung realisiert. Die Elektrodynamik dient hierbei dazu, zunächst eine grundlegende Verbindung zwischen Bauteil und Pulverwerkstoff herzustellen. Bevor die Pulverpartikel auf das Bauteil aufgesprüht werden, werden sie in der Spritzpistole elektrostatisch aufgeladen – meist mithilfe einer Elektrode an der Pistolenspitze (sogenannte Corona-Applikation). Das Bauteil wird vorab geerdet und zieht dann infolge des Ladungsunterschieds die aufgesprühten Partikel an. Es entsteht eine lose anhaftende Pulverschicht, die für mehrere Stunden stabil ist. An diesem Punkt schließt sich der Wärmebehandlungsvorgang an: Bauteil und Pulverschicht werden zusammen auf ca. 180°C erhitzt, wodurch sich die Molekülstrukturen des Pulvers zu vernetzen beginnen. Es schmilzt auf und geht in einen gelartigen Zustand über, bis schließlich die gesamte zu beschichtende Oberfläche von einem Film bedeckt ist. Die Temperatur wird dann konstant aufrechterhalten, und der Film härtet durch fortgesetzte Molekülvernetzung zur fertigen Pulverlackierung aus.
Wärmebehandlung im Konvektionsofen als Schwachpunkt des Prozesses
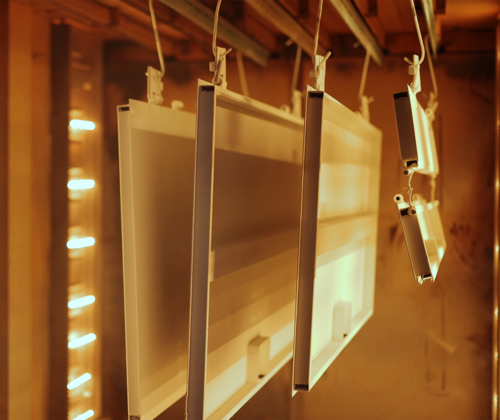
In jüngerer Zeit hat sich nun genau diese abschließende Wärmebehandlung vermehrt als Achillesferse des Gesamtprozesses herauskristallisiert. Durchgeführt wird sie bisher zumeist im gasbetriebenen Konvektionsofen, was allein schon angesichts der Gaspreisentwicklung und der CO2-Bilanz fossiler Brennstoffe Fragen aufwirft. Noch weitaus schwerer ins Gewicht fällt indessen, dass der Ofenprozess so viel Energie verbraucht, wie alle übrigen Teilschritte des Beschichtungsprozesses zusammen – und sich überdies das Verhältnis von Durchsatz und Energieaufwand so ungünstig gestaltet, dass sich schwerlich von einem wirtschaftlichen Prozess sprechen lässt, von Klimaschutzfragen ganz zu schweigen. Dieses ökonomisch-ökologische Prozessdefizit hat mehrere Gründe: Da das Angelieren im Konvektionsofen eine vollständige Durchwärmung des zu beschichtenden Bauteils erfordert, muss vor allem bei hohen Blechdicken eine lange Aufheizzeit in Kauf genommen werden. Die Verweilzeit der Bauteile im Ofen beträgt dadurch bis zu 40 Minuten, mit entsprechend negativen Folgen für die Energiebilanz. Zudem reduziert die lange Ofenzeit die Durchsatzrate, die zusätzlich durch den Luftstrom des Ofens beeinträchtigt wird. Da dieser Teile der elektrostatisch anhaftenden Partikel aufwirbeln und dadurch einen Pulverflug verursachen kann, müssen bei der Beschickung große Abstände zwischen den Bauteilen eingehalten werden. Andernfalls droht vor allem bei Farbbeschichtungen eine kritische Verunreinigung durch andersfarbige Partikel. Auch diese Maßnahme schützt indes nur bedingt vor Ausschussrisiken: Muss der Ofendurchlauf kurzfristig angehalten werden – zum Beispiel aufgrund einer technischen Störung – kann es infolge der Temperaturträgheit des Ofens zu einem Überbrennen der Beschichtungen und damit sogar zur Unbrauchbarkeit der Bauteile kommen.
In Anbetracht dieser Nachteile des Ofenprozess steht inzwischen für viele Beobachter fest, dass der Weg zu einem ökologisch und wirtschaftlich überzeugenden Pulverlackieren nur über die Erschließung alternativer Verfahren der Wärmebehandlung führt. Das gilt vor allem mit Blick auf die Aufheizphase, die verglichen mit anderen Prozessabschnitten den höchsten Energieaufwand verursacht und zudem das größte Pulverflugrisiko birgt. Gerade hier wird dringend eine Ausweichlösung benötigt, die den Energieverbrauch optimiert und durch Unterbindung kritischen Pulverflugs eine engmaschigere Wärmebehandlung ermöglicht.
Diodenlaser mit Ultrabreitstrahl als überzeugende Alternative
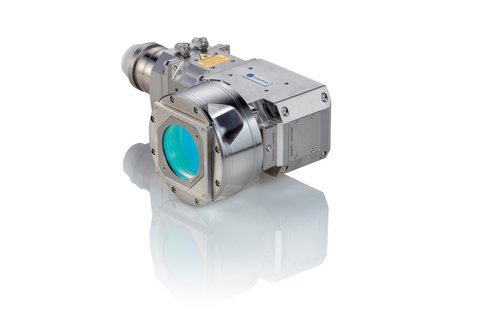
Mit dem eingangs erwähnten Aushärten mithilfe von Diodenlasern ist diese Ausweichlösung mittlerweile auch verfügbar. Das relativ neue Verfahren nutzt die Ultrabreitstrahltechnologie, die von Laserline ursprünglich für die Elektrodentrocknung von Lithium-Ionen-Batterien im Rolle-zu-Rolle-Prozess entwickelt wurde. Diese Bestrahlungstechnologie basiert auf den eigens hierfür konzipierten OTX Ultra Wide Spot Optiken und ermöglicht es, Strahlbreiten von 1,5 Metern und mehr zu realisieren. Das macht sie über die Elektrodentrocknung hinaus auch für andere Wärmebehandlungen großer Flächen interessant. Beim Aushärten von Pulverlacken kann diese Bestrahlungstechnologie wahlweise für Aufheiz- plus Haltephase – also den kompletten Aushärteprozess – oder nur für die Aufheizphase eingesetzt werden. Im letzteren Fall wird das Laseraushärten dem Ofenprozess vorgeschaltet und übernimmt das Aufschmelzen und Angelieren, während sich die Haltephase unverändert im Ofen vollzieht.
Großer Vorteil des Aushärtens mit Diodenlasern ist der punktgenaue und störungsfreie Energieeintrag: Während beim Ofenprozess das komplette Bauteil durchwärmt wird – und das über einen Luftstrom, der sich für die Durchsatzrate als nachteilig erweist –, wird beim Laseraushärten ein vergleichsweise „kalter“ Prozess realisiert: Die Bestrahlung mit dem passgenau dimensionierten Ultra Wide Spot erwärmt ohne Partikelaufwirbelung immer nur exakt jenen Bereich, der auch tatsächlich beschichtet werden soll. Die Ausgangsleistung des Lasers ist sofort in vollem Umfang verfügbar und wird bei laufendem Prozess binnen Millisekunden angepasst: Eine Closed-Loop-Regelung unter Einsatz eines Pyrometers, das kontinuierlich die Oberflächentemperatur des bestrahlten Bereiches erfasst und die Leistung des Lasers entsprechend adaptiert, stellt sowohl eine lückenlose Prozesskontrolle als auch den richtigen Energieeintrag sicher. In der Aufheizphase lässt sich mit diesem Prozessdesign eine 90-prozentige Erhöhung der Aufheizrate erreichen, was die Bauteil-Verweilzeit signifikant reduziert. Da die großflächige Bestrahlung mit dem Laser keinen Pulverflug verursacht, ist darüber hinaus eine engmaschigere Wärmebehandlung und damit eine deutliche Erhöhung der Durchsatzraten möglich. Last but not least ist durch die ständige Temperaturkontrolle ein Überbrennen der Beschichtung ausgeschossen. Muss der Bauteildurchlauf doch einmal komplett angehalten werden, lässt sich der Laser in Millisekundenschnelle abschalten und der Energieeintrag auf Null reduzieren – sieht man einmal von einer unkritischen Restwärme in der Umgebungsluft ab, die auf die Abstrahlung von Prozesswärme zurückgeht.
Einstieg über Hybridprozesse wahrscheinlich
Mit dem Laseraushärten steht Industrieanwendern also eine Verfahrensoption zur Verfügung, die insbesondere in der Aufheizphase alle kritischen Momente beseitigt und sich als ökonomisch sowie ökologisch überzeugende Alternative zum herkömmlichen Ofenprozess erweist. Hinzu kommt als grundsätzlicher Prozessvorteil die Nutzung des rein strombasierten Diodenlasers, der mit einem Steckdosenwirkungsgrad von mehr als 50 Prozent die höchste Energieeffizienz aller Industrielaser aufweist und per se einen Beitrag zum Klimaschutz leistet. Auch im Hinblick auf die Dimensionen der zu beschichtenden Bauteile gibt es keine industrierelevanten Einschränkungen, da sich mithilfe der Laserline OTX Ultra Wide Spot Optiken alle gängigen Bauteilgrößen abdecken lassen. Von dieser Flexibilität profitieren auch Hybridprozesse, bei denen der Diodenlaser dem Konvektionsofen vorgeschaltet wird – die Bauteilgröße wird dann lediglich durch die Dimensionen der Ofenanlage begrenzt. Solche Hybridprozesse dürften anfangs die Regel sein, da sie es ermöglichen, bestehende Ofenanlagen weiter zu betreiben und zugleich die Vorteile der neuen Technologie zu nutzen. Insbesondere die engmaschigere Wärmebehandlung des Laseraushärtens kommt dabei unmittelbar auch dem Ofenprozess zugute. Da nach dem Angelieren kein Pulverflug mehr droht, kann die höhere Beschickungsrate der Aufheizphase auch auf die Haltephase im Konvektionsofen übertragen werden. Das neue Verfahren optimiert über seine eigenen Vorteile hinaus also auch die Effizienz des Ofenprozesses und leistet somit auch in dieser Hinsicht einen Beitrag zur Verbesserung von Wirtschaftlichkeit und Klimabilanz.