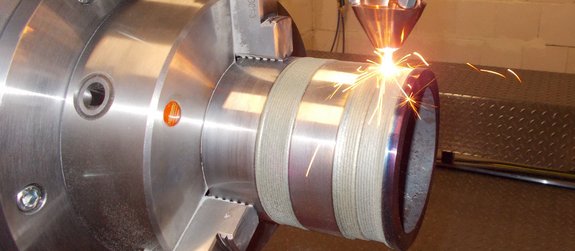
Membranwandbeschichtung durch Thermisches Laserspritzen
Antikorrosionsbeschichtungen von Membranwänden waren bis dato ein schwieriges Thema. Überzeugende Ergebnisse gab es nur um den Preis hoher Schichtdicken und starker Verformungen. Dass es auch anders geht, zeigt das Thermische Laserspritzen unter Einsatz von Laserline Diodenlasern.
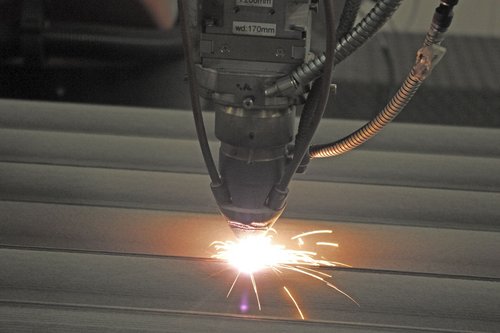
Chlor greift Metall an – diese Tatsache ist auch den Betreibern von Biomasse- und Müllverbrennungsanlagen nur allzu vertraut. Warum das so ist? Die Brennkesselwände solcher Anlagen bestehen aus wasserführenden Stahlrohrsystemen, die die Wärmeenergie des Kesselfeuers aufnehmen und an die Wasser-Dampf-Kreisläufe übertragen. Doch das Chlor im Rauchgas der Feuerung zersetzt die Rohre. Unbehandelt sind sie oft schon nach einem Jahr nicht mehr brauchbar. Dass das nicht wirtschaftlich sein kann, liegt nahe.
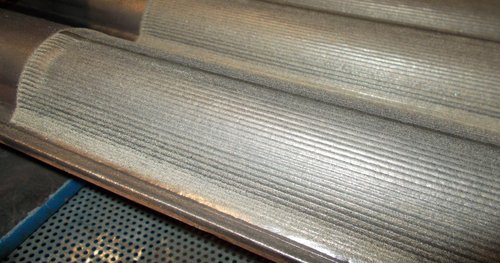
Viele Anlagenbetreiber setzen deshalb mittlerweile auf Antikorrosionsbeschichtungen. Der Aufwand hierfür rentiert sich bereits ab einer Verdopplung der Einsatzzeit – und es lässt sich sogar noch mehr erreichen: Abhängig vom aufgetragenen Material und der physikalisch-chemischen Belastung ist verglichen mit unbeschichteten Rohren eine Verdrei- bis Vervierfachung der Lebensdauer möglich.
Schwierig wird eine Beschichtung indessen, wenn Membran- oder Flossenwände im Kessel installiert sind. Bei diesem Rohrwandtyp sind die Kesselrohre durch Metallstege – die sogenannten „Flossen“ – miteinander verbunden. Diese Stege erzeugen eine geschlossene Wandfläche, was die Wärmeaufnahme optimiert. Die Oberflächengeometrie allerdings wird dadurch komplexer und bringt viele gängige Beschichtungsverfahren an ihre Grenzen. Speziell der Übergang vom gebogenen Kesselrohr zur geraden Flosse lässt die meisten Anwendungen scheitern. Zielführend einsetzen ließ sich in der Vergangenheit nur das klassische Laserauftragschweißen. Es bewältigt auch kritische Oberflächengeometrien und erzeugt stabile Schichten, die metallurgisch mit dem Grundwerkstoff verbunden sind.
Doch so erfolgreich das klassische Laseraufragschweißen auch war – zwei gravierende Nachteile mussten stets in Kauf genommen werden: Zum einen waren die Beschichtungen nicht so korrosionsbeständig wie gewünscht, da sich Schicht- und Grundwerkstoff beim Schweißen stark vermischten. Um dies auszugleichen, wurde mit höheren Mindestdicken gearbeitet. Und zum anderen verursachte der hohe Wärmeeintrag Materialverformungen, die kostspielige Nachbearbeitungen notwendig machten.
Dem Beschichtungsspezialisten Häuser & Co. GmbH ließen diese Nachteile keine Ruhe. Ausgehend von einer selbstentwickelten, patentierten Plasmaspritztechnologie mit nachgelagerter Wärmebehandlung entwickelten die Duisburger ein neues Verfahren, das mit Laserline LDF 6000-100 Diodenlasern arbeitet und die Verfahren des Thermischen Spritzens und des Laserauftragschweißens kombiniert: Das Thermische Laserspritzen. Bei dieser Beschichtungstechnologie verschmilzt der Diodenlaser – ähnlich wie beim Auftragschweißen – den pulverförmigen Beschichtungswerkstoff mit der Oberfläche des Werkstücks und erzeugt so eine metallurgische Verbindung. Da die gleichmäßige Energieverteilung innerhalb des Diodenlaserstrahls ein ruhiges Schmelzbad und eine optimierte Eindringtiefe erzeugt, vermischen sich Schicht- und Grundwerkstoff nur wenig, sodass die Schichten weit korrosionsbeständiger sind als auf herkömmlichem Wege geschweißte Beschichtungen. Auch die komplexen Oberflächenstrukturen und speziell die kritischen Übergangsbereiche zwischen Rohr und Flosse stellen kein Problem mehr dar. Denn da der Laserstrahl innerhalb von Millisekunden feinabgestuft reguliert und aus wechselnden Richtungen auf das Werkstück gerichtet werden kann, passt er sich beim Aufschmelzen exakt an alle Oberflächenstrukturen an. Verformungen kommen deshalb nur sehr selten vor. Endergebnis sind homogene, fast porenfreie Schutzschichten. Sie können in kurzen Prozesszeiträumen realisiert werden und bedürfen meist keiner Nachbearbeitung.
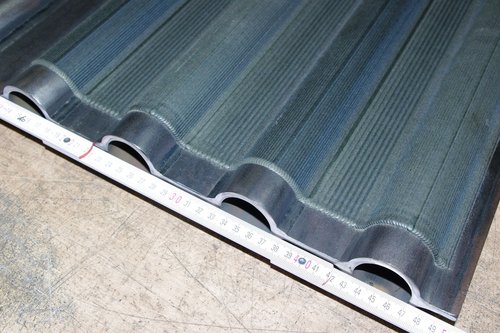
Fazit:
Das Thermische Laserspritzen arbeitet materialschonender als bestehende Verfahren, es ist präziser und ermöglicht eine wirtschaftlichere Prozessführung. Bekannte und bewährte Beschichtungswerkstoffe wie Inconel 625, Hastelloy C oder Stellite 21 lassen sich auch hier ohne Einschränkung einsetzen. Darüber hinaus eignet sich das Verfahren auch für andere Beschichtungsanwendungen, zum Beispiel für die Beschichtung industrieller Armaturen und Antriebswellen, für die Reparatur gebrauchter Dichtplatten, Spindeln und Walzenzapfen sowie nicht zuletzt für den maritimen Bereich.