
Beam Shaping done right
Without optics, no laser system! What may irritate the layman would actually be self-evident to the expert. The expert knows that the output of a laser beam source in and of itself is not capable of initiating a process.
Diode lasers and their applications - part 7: Beam Shaping
What the source emits is concentrated energy, but it needs to be put on the right track. The magic word here is beam shaping, and nothing works without optics. Diode lasers are no exception. They cannot be released onto a workpiece without optics, even if they are fiber-coupled. The fiber guides the beam to the workpiece, but does not usually shape it unless special fiber optics are used. However, that would be a wholly different topic.
In commercially available diode laser systems, beam shaping takes place via an optical system consisting of lens and mirror elements — the so-called processing optics. As the name suggests, these optics shape the laser beam in such a way that it is suitable for the planned material processing. In other words, it turns what the beam source spits out into a beam with which the user can actually do something. Two points are crucial here. First, it is important that the beam is suitable for welding, brazing, hardening or coating. Second, it must match the nature of the workpiece.
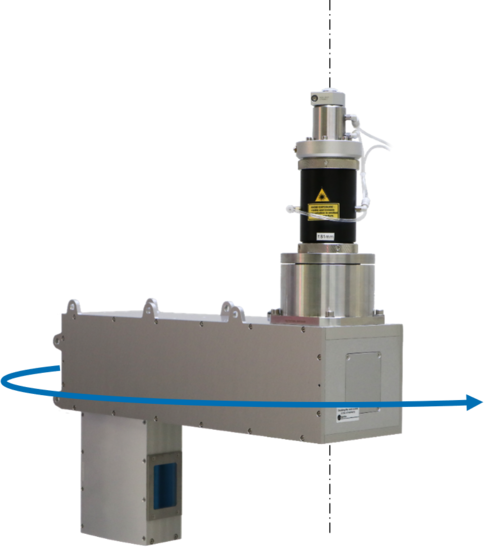
Classic Example
Here is a classic example. A beam meant to be used for hardening applications must be particularly homogeneous. The optics must therefore ensure that the energy distribution is as uniform as possible. Special homogenizing optics are available for this purpose, which further optimize the inherently homogeneous diode laser beam. In addition, the beam must be suitably dimensioned as well. For example, if a cam is to be hardened, the spot should not be wider than the cam itself, otherwise it would literally miss the mark. Optics take care of that, too. They adjust the spot size and, if in doubt, even do so while the process is running. Laserline offers motorized zoom optics that can change the spot during the machining process, thereby always ensuring the perfect size.
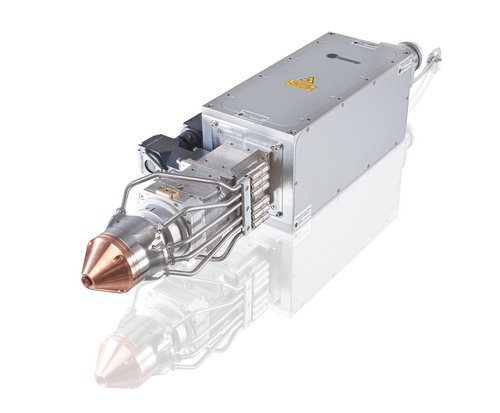
The Geometry
Not only does size matter, but so does geometry. The question arises whether the spot should be rectangular, round or linear, a choice whose significance will become apparent during coating. Here, rectangular wide beams are often used across the board because they promise effective machining with high coating rates. However, a rude awakening regularly occurs when components are filigree and sharp-tapered, as in the case of machine knives. In this case, the wide beam often delivers so much energy to the component that the self-quenching no longer works and, in the worst case scenario, the cutting edges melts off. Those who rely on narrow, focused round spots here and only hit the stronger surfaces with the wide beam have a clear advantage. In addition, it should be possible to switch flexibly between the two spot shapes. High-quality optics such as those from Laserline make this possible.
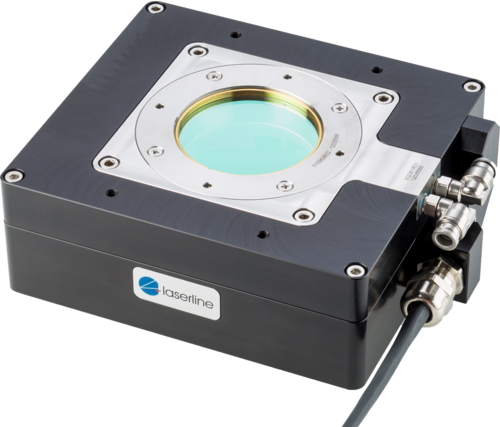
Beam splitting by multi-spot optics
And then there are those very special cases wherein a simple beam is not enough, however well it may be shaped. In the brazing of hot-dip galvanized sheets, for example, processes with normal spots run so unsteadily that you have to reduce the process speed to keep the number of spatters reasonably manageable. The solution is an award-winning innovation from Laserline: beam splitting by multi-spot optics. These turn a classic round or wide beam into a main spot with two pre-spots that remove the galvanization in the seam area, thus calming the process.
The list of examples is of course somewhat long. But it should already be clear to anyone by now why we said what we said at the beginning: without optics, no laser system! It simply cannot be done without them, because the world of applications is much too complex. And wouldn’t it be a shame not to take advantage of the possibilities? Sure, in purely theoretical terms, you might as well just fix the fiber in the area near a workpiece, turn the knob on the beam source a bit, and something would happen. But as the ancients said: "Quidquid agis, prudenter agas et respice finem" (= whatever you do, do it wisely and consider the end result).
Learn more about our processing optics.