
Brazing with diode lasers
In the second part of our little series about diode lasers, we have already dealt with metal welding as application emphasis. A further joining technology that can be realized with diode lasers — and about which we report today — is brazing. This method was adopted due to its high aesthetic quality, mainly in the series production of vehicle bodies. Moreover, it is also used for joining components that cannot be welded due to dissimilar melting temperatures.
Diode lasers and their applications - Part 6: Brazing process
We start with the basic principle of laser brazing: with this method, two joining partners are connected by a filler material: the solder. For this, the brazing solder — e.g. copper-silicon-wire — is melted with the diode laser and then allowed to flow into the joint gap between the two components. There it connects with the surface of the workpieces and gains, after cooling down, the required firmness. The melting temperature of the filler material is lower than that of the components. Therefore, during processing, only the solder melts, as the joining partners are merely warmed up.
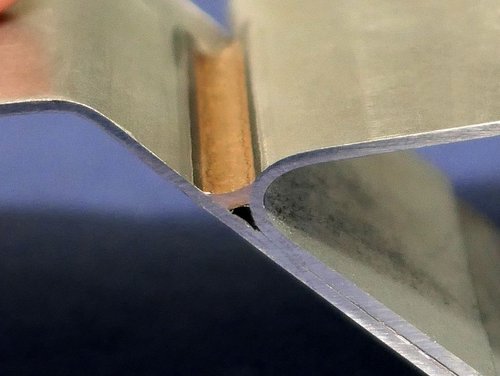
Brazing works with diode lasers
Brazing works with diode lasers to create a specific, smooth and clean seam with homogeneous junctions by filling up the joint between the two components. Thus, laser brazing is above all predestined for visible seams and requires no or little post-processing as, for example, the grinding of the solder seams. Therefore, the application wholly suits the mass production of vehicle bodies that must withstand high optical requirements. After cleaning the processed area, the car bodies for the most part can directly be lacquered. Laser brazing also proves itself in the mixed construction. Components from different raw materials sometimes make the welding difficult or impossible because of the rather dissimilar melting points. Aluminum and steel, for example, can be joined successfully in most cases only by brazing.
Triple-spot module - the solution for brazing hot-galvanized sheets
When joining galvanized sheets, laser brazing succeeds from the get-go. Diode lasers mostly installed in special brazing robots create calm molten pools and therefore seams with high aesthetic quality. A little more difficult at first was the treatment of hot-galvanized sheets that are used more and more in the automotive industry. The manufacturers reported micro spatters and wavelets (areas where the solder exceeds the intended seam size) which reduced the process speed. But a solution was also found for this problem. Together with VW and Scansonic, Laserline has developed a so-called triple-spot module with OR spot design (optimized rectangular spot).
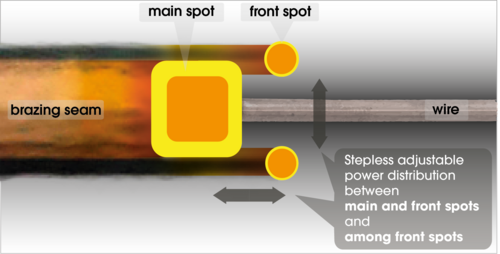
In front of the square main spot, there are two side spots which ablate the galvanizing at the edge of the brazed seam. This concept was as groundbreaking as trendsetting: the main spot was able to immediately melt the solder and create the desired seam quality. Thanks to the initial zinc ablation, the brazing process was calmed down, such that the method could be carried out not only with its known quality, but also with its familiar speed. Since 2016, this effective solution has been used worldwide in several Volkswagen production lines for the laser brazing of hot-galvanized roofs and tailgates.
If that isn’t enough, motorized triple-spot modules make the method even more flexible by adjusting the spots during the running process to the movements of the optic. Via a processing robot, the power distribution and distance of the pre-running spots are precisely set. This eases programming at 3-D-applications, such as the brazing of tailgates. Furthermore, with the optional switching-off of the front spots, one can flexibly switch forth and back between monofocal brazing for galvanized and trifocal brazing for hot dip galvanized coatings. This choice is especially advantageous in systems that are meant for the brazing of different vehicle models’ roofs.
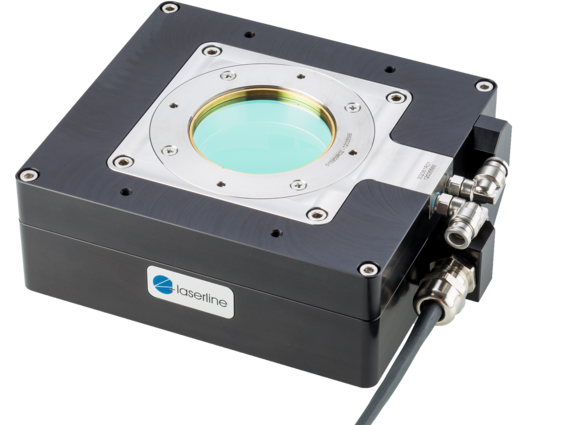
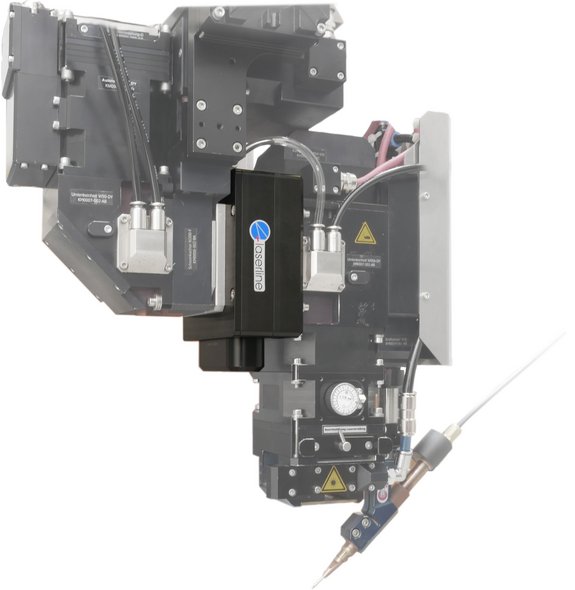
The means of choice
So, even when it is about the joining of two components, the diode laser is still the most appropriate tool. At soldering and brazing, it does not only create smooth, dense and clean seams, but it also ensures high process speeds and low heat inputs. Even hot-galvanized sheets that used to be a challenge for the brazing technology until recently can now be joined efficiently and cost-effectively by means of the triple-spot module. Yet again, it can be confirmed: All good things come in threes.
More information about brazing with diode lasers.