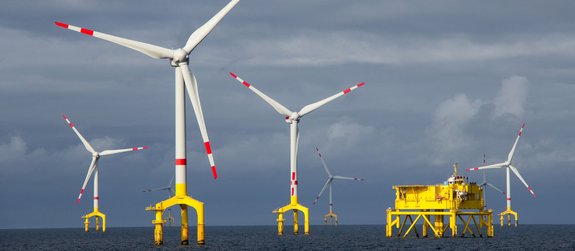
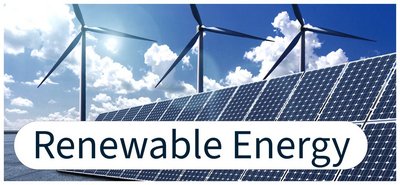
Coating of wind turbine plain bearings
Diode laser-based coating of wind turbine plain bearings is becoming increasingly popular. The main reason for this, in addition to the cost-effectiveness of the process and the outstanding quality of the coatings, is that this process does not require the use of lead-containing copper-tin alloys, which are harmful to health.
Diode laser-based cladding increases service life and allows process speeds to be increased
With the adoption of the EEG amendment, the German government has increased the expansion goals for wind power plants: On land, the stated aim is an increase to 115 gigawatts (GW) by 2030; in the offshore sector, capacities of 30 GW by 2030 and 70 GW by 2045 are planned. This widespread expansion of wind energy will be crucial to the energy transition. Therefore, it is all the more important that key components such as plain bearings are not only of high quality and durable but are also manufactured in an energy- and resource-efficient way. In this context, the coating of plain bearings plays a key role: It reduces frictional resistance and thus increases the service life of the components. So far, wind turbine plain bearings have mostly been coated using the centrifugal casting process or oven coating. However, these processes have some weaknesses: They are energy intensive and often based on combustion of natural gas and require a significant amount of material to achieve high-quality results. Meanwhile, laser cladding or laser deposition brazing turned out to become an alternative: It not only impresses with lower energy and material consumption, but also with higher robustness, thinner, well-defined, and lead-free coatings of the highest quality.
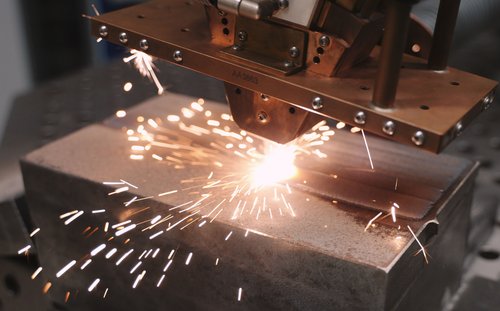
High-power cladding with diode lasers
These results are made possible by the use of high-performance processes that minimize the heat input into the workpiece. For wind turbine plain bearings, non-ferrous metals and copper-tin alloys are commonly used to coat the outer diameter - i.e. the shaft - and are applied in a single-stage process at process speeds of several meters per minute. This creates a durable and robust bonding between the base material and the coating materials. A key advantage of laser cladding is its flexibility, which allows, for example, to adjust the spot size and geometry as well as the laser power to customer’s requirements.
Spoilt for choice: Wire or powder
The choice of coating material - powder or wire - also has a decisive influence on the precise process parameters. With wire-based laser cladding, typical deposition rates are 0.5 kg/h per kW of laser power. Additionally, Laserline offers various multi-wire and hot-wire applications, as well as application-specific customized solutions. A major advantage of the wire-based method is that no waste material is produced. However, the range of materials is limited, which restricts the customization options.
Powder-based laser cladding, on the other hand, excels with a diverse product range. With a powder efficiency of up to 95%, there is minimal material loss in this process as well. The laser beam also melts the powder evenly, resulting in a very smooth melt pool. Wide beam nozzles have proven to be highly advantageous, as they allow a particularly fast coating or a higher material application within the same time frame. In this case, the application rate is 133 g/min (or 8 kg/h), so that layers of approx. 1.4 mm thickness can be built up at a speed of 100 to 200 cm²/min. Moreover, the use of a round spot with a diameter of 6 to 12.5 mm and an output of 5 kW is possible. The application rate here is 45 g/min (2.7 kg/h), so that layer thicknesses of around 1 mm can be achieved at a process speed of 1.5 m/min. Additionally, there is the option of coating the inner diameter of the plain bearing. Laserline provides various solutions here.
High-speed coating
In terms of development, the sky is not the limit yet. In fact, continuous efforts are being made to further increase process speeds: Currently, deposition rates of over 10 kg/h can already be achieved at process speeds of up to 200 m/min, which is equivalent to a surface application rate of up to 10 m²/h. These high processing speeds are made possible by increasing the laser power to over 20 kW. At the same time, diode laser-based cladding supports the build-up of particularly thin layers with thicknesses starting at 0.2 mm, which are nevertheless highly stable. (Reasons for this include minimal pore formation during laser coating and the creation of robust fusion metallurgical bonding between the components and the coating material). Since the powder efficiency of high-speed laser deposition brazing is up to 90 percent and the material usage is lower due to the low coating thicknesses compared with conventional traditional laser cladding, this approach is a highly sustainable option.
Improved process and component monitoring
This brief description already highlights that diode laser-based coating offers many advantages: Reduced energy consumption and material savings make the production of wind turbine plain bearings significantly more sustainable; the avoidance of lead-containing substances makes the process more health-friendly and environmentally friendly. Another advantage: The reduced need for post-processing speeds up production considerably.

The process has now been tried and tested and is already being used in serial production. New, comprehensive methods of process and component monitoring now also enable more reliable defect detection and quality control. With the help of software-supported infrared cameras and systems for measuring process emissions, the occurrence of pores and other material defects can be largely prevented. If irregularities do occur during the coating process, the systems detect them, and such component can be separated afterwards. Coaxial monitoring of process emissions also facilitates subsequent fault analysis. However, the collected data can be used for more than just quality control. In the future, it will also be used for Industry 4.0 and smart factory applications.