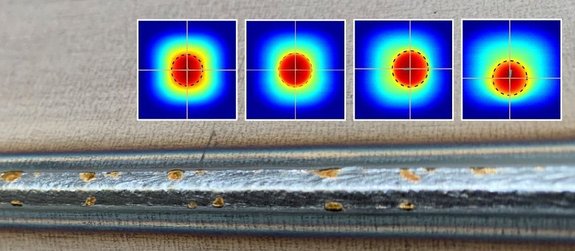
Diode lasers improve gap bridgeability
Bridging wide gaps is a classic challenge in metal welding. It may arise in car body construction as well as in machine building, pipeline construction or shipbuilding.
Laser joining with multi-spot module replaces GMAW welding
The primary solution has long been gas shielded metal arc welding (GMAW) – a classic joining technology that uses an electric arc to melt the workpieces. This welding solution is inexpensive to purchase and has certainly proven itself for bridging wide gaps. However, there are weaknesses in terms of seam optics and process efficiency: in addition to comparatively slow welding speeds, users often struggle with considerable distortion due to the high heat input. Often, time-consuming and costly straightening is required. Added to this are cost-intensive rework operations to repair unclean seams.
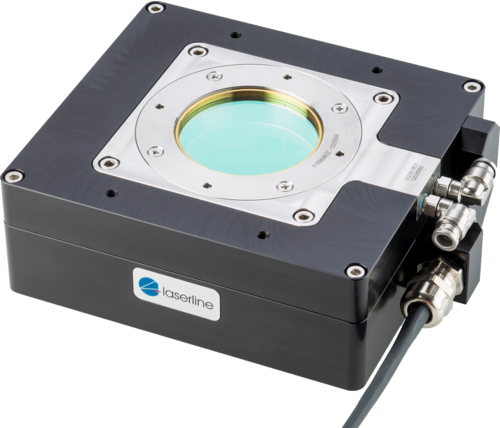
New processing options for joining symmetrical and asymmetrical seams
Overall, joining processes can be realized more effectively by diode laser-based cold wire welding with multi-spot optics from Laserline. For this purpose, a multi-spot module splits the collimated laser beam and generates in this way a smaller inner spot, superimposed by a larger, rectangular outer spot. In the welding process, the inner spot melts the joints of the workpieces and the supplied cold wire, which serves as an additional filler material for the seam. The wide outer spot improves gap bridgeability and, due to its low penetration depth, produces a calm weld pool without spatter formation. Compared to pure laser beam welding, the multi-spot optics and cold wire insert allow gaps of one millimeter instead of the usual 0.1 to 0.3 millimeters to be bridged. The result of the welding process is smooth seams without edge notches, which no longer require any post-processing. The seam cross-section can also be optimized by specifically adjusting the spot size and power distribution. The spot-in-spot configuration opens up interesting processing possibilities, especially when joining asymmetrical seams: the outer spot can be continuously shifted, thus enabling dynamic adaptation to changing seam geometries while the process is running. This supports one-sided melting in the case of thickness jumps, which is desirable for example for tailored blanks.
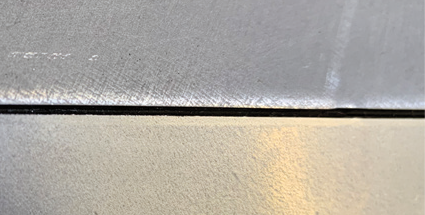
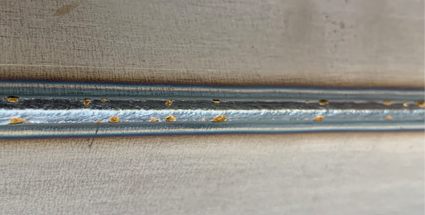
Process video: Laser joining with spot-in-spot design
By using a processing optics with Laserline Multi-Spot module and cold wire, gap dimensions of up to one millimeter can be bridged.
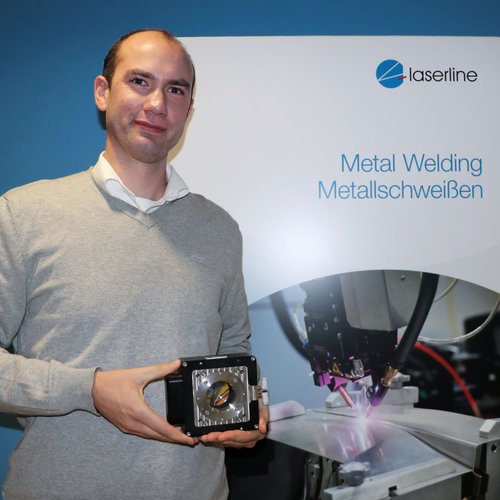
High process speeds, very low distortion
With the spot-in-spot design, the desired seams can also be realized significantly faster: Laser powers in the multi-kilowatt range allow the process speed to be tripled compared to GMAW welding, thus ensuring higher output in industrial series production. In addition, the increased feed rate reduces heat input into the workpiece, effectively preventing material distortion. Overall, laser systems with spot-in-spot focus from Laserline are thus a real alternative to GMAW welding that not only achieves better results in terms of seam quality, speed and cost-effectiveness, but also offers new processing options when joining asymmetrical seams. The multi-spot modules can be easily integrated into processing optics of a Laserline LDF series laser system. When selecting individual application configurations, the diode laser manufacturer from Mülheim-Kärlich is happy to provide everything from detailed advice to test runs in the company‘s own application laboratory.
Read more about the multi-spot module!