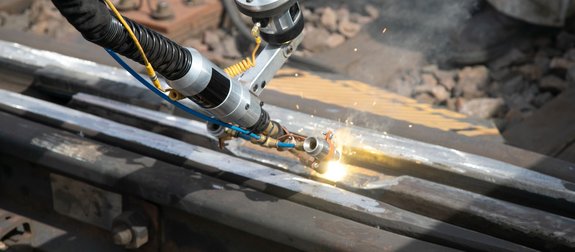
Durable railway line repair on track with mobile laser
New approaches enable diode-laser-based additive welding of rail track and points even under extreme weather conditions
The service lifetime of welded repairs to the rail track network has previously left a lot to be desired. One of the key reasons for this is the inappropriately high heat transfer of traditional welding techniques, often resulting in damage to the underlying structure of the steels used. Longer service lifetime as well as gains in process speed can however be realized with diode-laser-based additive welding – a fresh system approach means that repairs can now even be made in the field and directly on the track network.
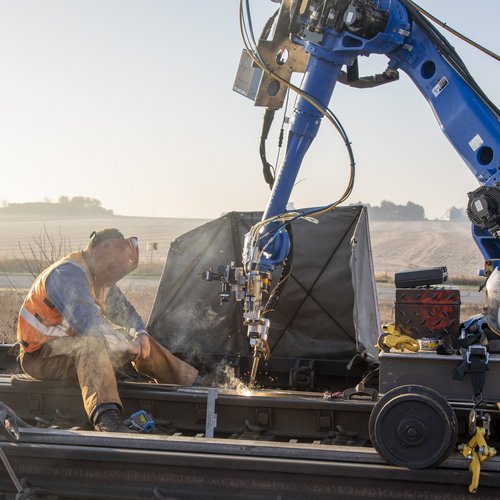
Repair welds to defective or damaged switch points are among the most common tasks of rail network maintenance. Daily rail traffic as well as weather-related factors both contribute to everyday wear and tear and so to corrosive erosion of the (so-called) frogs, guard rails and even to the points themselves. Even though frog components are today made from an extremely resistant steel grade (austenitic high manganese steel or AMS steel), this has only served to reduce the frequency with which these components have to be repaired. Despite this gain, switch point components still retain the shortest repair and replacement cycles when compared to straightforward track. One significant but disappointing aspect of the required maintenance is the service lifetime of repair welds made to switch point components in relation to durability when new. Repeated repairs are usually necessary within six months, at the latest within twelve months’ time. For stretches with heavy traffic, the cycle may be only a matter of weeks, and after three to four such cycles it is often necessary for a complete replacement. All of this leads to high construction costs and the associated downtime for the rail network.
High heat input during MIG welding impairs service life of repairs
The relatively short service life of repair welds is due in no small part to the predominant repair welding process in the track construction sector – metal inert gas (MIG) welding, which is usually performed manually. It belongs to the group of arc welding processes, makes extremely economical welding processes possible for a large number of metallic materials and has accordingly been used for decades in a wide variety of metal processing areas. However, the high heat input of the process is especially critical when processing AMS components. To prevent damage to the steel structure, the application of successive additive layers must be delayed so that the temperature of previous layers does not exceed a certain value – existing layers simply require sufficient time to cool down before the next layer is applied, but this results in comparatively long repair times. In addition, the welding process as a whole is quite complex and usually requires many years of welding experience to be carried out correctly. Since there are virtually no quality control options for manually performed MIG welds, welding defects and excessive heating of the intermediate layers repeatedly go undetected – with negative consequences for the service life of the weld.
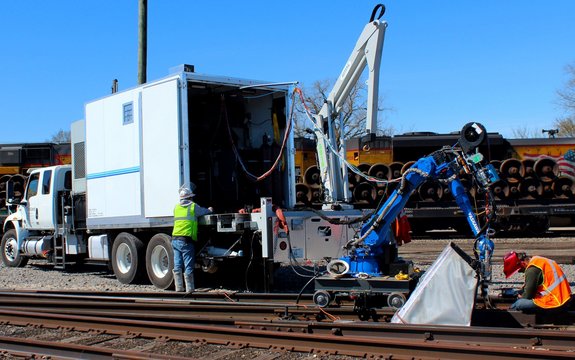
Economically viable repairs using diode-laser-based additive welding
In order to achieve greater durability of the unavoidably necessary rail track repairs in the future – and thus also prolong the repair and replacement cycle – a search has already been on for some time for welding technologies that provide for a more precise process management together with a more controllable heat input into the workpiece. A prime candidate for fulfilling these requirements is laser additive welding, or laser metal deposition, an approach widely appreciated for also affording a high degree of flexibility, for example for the application of wear-resistant coatings as well as for the repair of damaged metal tools and components. For these very reasons, we see that the laser cladding approach has quickly found favor and is already broadly utilized in the automotive, heavy industry and in agricultural machinery sectors.
The treatment process runs similarly to that of electric arc welding, although of course the requisite heat input is provided by a laser. This results in a hard-wearing repair coating that is metallurgically bound to the workpiece. When compared to traditional MIG welding we find that short and intensive heat inputs are already sufficient, thus avoiding unnecessary overheating of the base material and at the same time significantly speeding up the layering process as a whole. Moreover, the requisite heat input at each section of the workpiece can be finely adjusted in real time within the running process.
In general, best results are achieved with fiber-coupled diode lasers – the so-called ‘top hat’ beam profile of this laser type contributes to a uniform energy input and so too to a consistent surface treatment.
Mobile laser welding unit optimizes track repairs
Despite these significant advantages, however, laser metal deposition has hardly been used in track repairs. The main reason for this was the harsh application environment: track repairs are carried out in the field, often in remote locations that are difficult to access. The entire welding equipment must therefore be transported to the respective site, which is usually almost inconceivable with conventional industrial laser systems – consisting of laser system, cooling, processing robot and control system. To make matters worse, the highly sensitive laser technology is, in the field, exposed to critical weather factors such as heat, cold, rain and humidity. This can have a lasting impact on the functionality of a laser system.
This challenge has however been met by specific development work made by two US companies, laser technology specialist Titanova and rail track constructor Holland LP, whose collaboration has resulted in the so-called ‘Holland Automated Manganese Refurbishment’, a repair weld solution designed for track construction projects. The core element of this solution is a 6 kW Laserline LDM 6000 high-power diode laser that is connected by cable to a Yaskawa robot arm and a Laserline OTS-5 optical headthat is specificallydesigned for coating applications.
By modifying a conventional road-going truck with additional undercarriage for autonomous movement over the rails, the entire system complete with laser, robotics and optics can be efficiently transported to any intended operational site to/on the rail network. On location, the robotics and optics, mounted on a special bogie, can then be hoisted from the truck via a dedicated fixture, and moved independently over the rails to a nearby point of repair.
This system can be reliably used even under extreme weather conditions – the laser source is protected from the elements within the truck but remains connected to the robotics and optics via the cable. In order to guarantee reliable operation, extremes of temperature in the field are accommodated for with modifications such as additional ventilation ducts and a high-performance 12 kW cooling system.
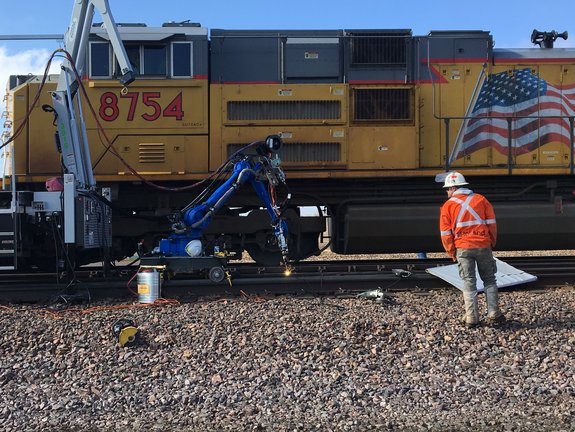
The globally unique solution concept was tested in practice for the first time in March 2019. The results are overwhelmingly positive: All necessary process steps can be carried out up to three times faster with the mobile laser device when compared with manual MIG welding, and this includes time for material removal prior to, and dressing (grinding) the repair after the actual coating process. The repair welds thus realized have been proven to have a significantly longer service life than MIG welds. The new diode laser-based solution is therefore a significantly more economical option for repair welds on rails and switch components such as points, frogs and guard rails.
Last but not least, the concept also scores points in terms of user safety: As the process is automated, no one has to remain in the direct vicinity of the workpiece. The track workers can therefore move away from the track bed when a train approaches and are also no longer permanently exposed to harmful fumes as is the case for manual MIG welding. In addition, the welders no longer have to remain in a stooped sitting position above the rails during welding work, something that often leads to back problems.
After the solution achieved excellent results in all test runs and impressed across the board, a five further units are now in use across the US rail network. In the future the technology is scheduled to be rolled out worldwide – a first system has already been successfully set up for Australia, and further projects in Europe and Canada are nearing completion.
This article was first published in the "Der Eisenbahningenieur" magazine in the May 2023 issue.