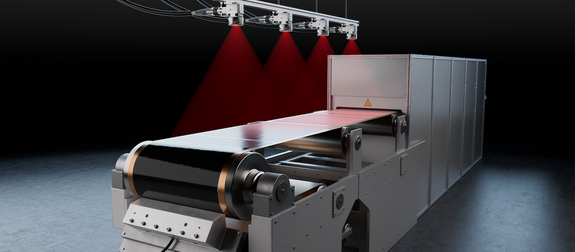
Energy and quality turnaround for drying processes
Diode lasers with an ultra-wide beam are set to replace gas-based convection ovens
Replacing convective drying with laser drying? In times when highly efficient electrified solutions are sought in the face of gas shortages and rising energy costs, this could become the standard. Diode-laser-based drying processes in roll-to-roll mode, optimized by a revolutionary beam shaping technology, bring excellent throughput rates and results as well as making a significant contribution to gas phase-out and climate protection.
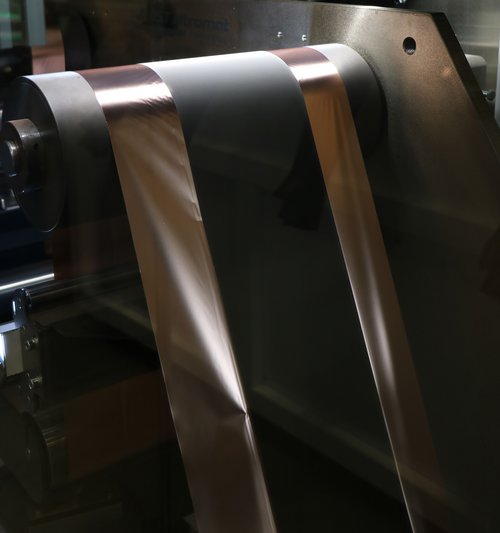
Laser-based drying processes have played a low-profile role in industry for a long time. Diode-laser-based drying processes in particular have been discussed as an alternative to the widespread convective drying, and even successfully implemented – Heidelberger Druckmaschinen, for example, began using Laserline diode lasers as early as 2012 to dry offset ink layers in a roll-to-roll process. Nonetheless, convective drying, comprising gas-driven continuous ovens 100 to 200 meters long, have long dominated most fields of application from print to packaging and initially remained so in the market. A major reason for this, as is the case for many other industrial sectors, was the very low cost of natural gas as an energy source over a long period of time. These ovens promised an extremely economical process control, yielded a positive effect on production costs and thus enabled attractive margins. However, the CO2 footprint of gas-based drying and its contribution to global warming was neglected – and thus also the long-term consequences in terms of the follow-up costs of climate change.
Diode lasers as the ideal solution for the electrification of the drying process
The cost-driven scarcity of fossil fuels and the increasing importance of climate protection measures have meanwhile triggered a rethink for industrial drying. In paving the way towards CO2-neutral industrial drying, electrification of the drying process is the order of the day, coupled with targeted optimization of process efficiency. By enabling the desired electrification, the diode laser is regarded as the ideal technical solution for drying processes, and in doing so making a comparable contribution to that made by the electric motor to the transport sector and the heat pump to the building sector. The semiconductor-supported direct conversion of mains electricity into laser radiation (‘direct power to light’) promises – assuming electricity from renewable energy sources – the liberation of the process from fossil fuels and thus an energy turnaround in industrial drying. With an electrical efficiency of over 50 percent, Laserline high-power diode lasers also achieve the highest energy efficiency of all commercially available industrial lasers and thus make their own not insignificant contribution to improving the CO2 balance of industrial processes.
Precise energy utilization and optimum process control
Another fundamental advantage of drying with diode lasers is the precise utilization of energy within the process. Thanks to the ability to both focus the laser beam and to switch it on and off within milliseconds, only as much energy is introduced into the workpiece as is needed for the desired drying process. This is not only far more energy efficient than the rather undifferentiated drying inside a convection oven, it is also far more energy efficient than drying with infrared lamps. While the latter is sometimes considered a second electricity-based alternative to the gas oven, and indeed offers greater simplicity than laser drying in terms of process design, their lack of focusability directly results in a noticeably reduction in efficiency. Additional disadvantages include not inconsiderable absorption of the lamp radiation by the water vapor produced during drying, the requirement for small working distances, and sub-optimal temperature control of the process. In contrast, typical diode laser wavelengths of 1000 nm easily penetrate water vapor, the ability to focus the beam directly translates into flexible working distances, which in turn make better air flow management possible, and high-precision temperature control can be achieved with the aid of thermographic cameras. Lastly, diode lasers are also advantageous for cleanroom applications as a fiber-coupled beam source can be placed outside of the cleanroom – an option that is not available with conventional infrared lamps.
New drying optics enable worldwide unique beam widths
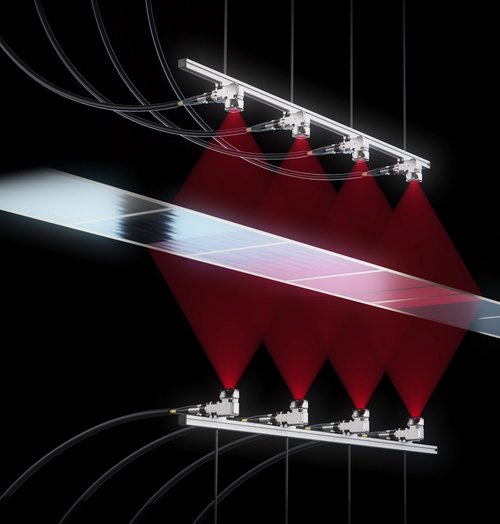
In addition to the general process advantages of the diode laser, there have now technical developments in beam shaping that enable industrial drying processes of exceptional energy efficiency. Whereas drying paths of 200 to 300 mm width were previously usually realized, beam widths of over 1.5 meters can now be achieved with the aid of new Laserline drying optics. In combination with the high energy efficiency and the high-power classes of Laserline diode lasers (>20 kW), this ultra-wide-beam technology enables extremely effective drying processes, particularly in the classic roll-to-roll process, and opens up enormous energy-saving potential. In test runs with pure laser drying ovens, it was possible to save up to 85 percent of the energy required by convection ovens. In hybrid solutions, in which a laser drying oven is installed upstream of a convection oven, the feed rate of the convective drying process could be doubled, also enabling very considerable energy savings and at the same time significantly increased throughput. With the aid of diode lasers, significant progress can thus be made towards CO2-neutral industrial drying.
Cross industry interest
Thanks to these technical optimizations and the advantages gained, diode-laser-based drying is now attractive for numerous areas of application in which only convection ovens have previously been used. For example, laser-assisted drying within a roll-to-roll process could also be used effectively for drying polymer dispersions in the production of adhesives and plastic coatings. Major benefits are also expected in the field of printed electronics, as the metal particles of printed conductive tracks can be bonded more effectively with lasers than by convective drying, and which additionally promises to improve the conductivity of the circuits. This is of interest to the plastic film industry, among others, where electronic security labels or polymer solar cells are applied and dried in a roll-to-roll process. The same applies to the production of printed sensors as used, for example, to measure the expansion of plastic films. All of the respective laser-assisted drying processes are still currently in the qualification phase, but will be made available in the near future.
Successfully early adoption for battery manufacturing
Diode-laser-based drying with ultra-wide-beam technology is already being implemented with great success in the production of lithium-ion batteries, in particular important for electric vehicles. In this manufacturing environment, diode lasers perform the task of drying the electrically conductive paste (slurry) that is applied to the copper foils of the battery electrodes. As part of the publicly funded research project IDEEL (Implementation of Laser Drying Processes for Economical & Ecological Lithium-Ion Battery Production), the goal of which being the consistent development of this production process, laser-drying of anodes and LFP cathodes in a roll-to-roll process was demonstrated for the very first time in a process utilizing Laserline diode lasers. In addition to pure laser drying, hybrid drying with laser and downstream convection oven has also been successfully tested, meaning that it will also be possible to subsequently implement a diode-laser-based process within existing production plants. As drying processes account for around 30 percent of the overall energy requirement for battery production, laser-based drying is a decisive step forward here, both ecologically and economically. The energy turnaround in drying thus also makes a valuable contribution to the phase-out of gas and to climate protection in this area of application.
Learn more about laser drying.