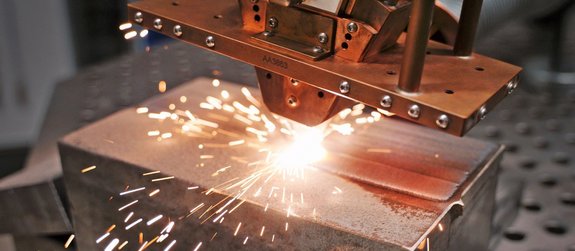
Laser Cladding Today: Status of Technology (Part I)
Coating, repairing, generating — all industry-typical processing methods that can be handled with a single process: laser cladding. This flexible coating process is a real all-rounder. It delivers outstanding results in all three areas of application which explains its successful use today on a broad scale: from automotive construction to heavy industry and agricultural engineering.
Part 1: The basics of laser cladding
And there, laser cladding is increasingly replacing conventional technologies. But this is by no means the end of the story: thanks to further technological developments, the comparatively new process can conquer new areas of application. Regardless of whether you are an expert or a layman, it is worth taking a look at the current state of the art, which is reason enough to take a closer look at this process in our four-part series: “Laser cladding: The current state of the technology”

Basic Functionality
Before we turn to the strong points of laser cladding, let us first take a step back and take a more detailed look at the basic mode of operation. Here, the laser simply acts as a heat source. It melts the surface of the workpiece. A coating material is inserted into the molten pool, either as powder or wire. The material is also melted, so that the surface and coating material are fused. After cooling, a solid fusion compound of two metals remains, which is also referred to as a metallurgical alloy.
The type of fusion between the base material and coating material is already one significant advantage of laser cladding. This is because metallurgical joints are very robust and have a long service life. By comparison, in thermal spraying, the coating material is heated and projected onto the component’s surface at high speed. As a result, the coating merely adheres by way of mechanical bonding. It easily flakes off in the event of hard impacts and shocks. Better results are achieved by coatings applied by arc welding. Although these processes use an arc rather than a laser as the heat source, the principle is similar. Here, too, stable, metallurgical bonds of high durability are produced. At the same time, however, the heat source itself is a major disadvantage. This is because the high energy input of the arc can deform the component, which subsequently requires complex straightening. In addition, precise, thin coatings can hardly be realized in this way.
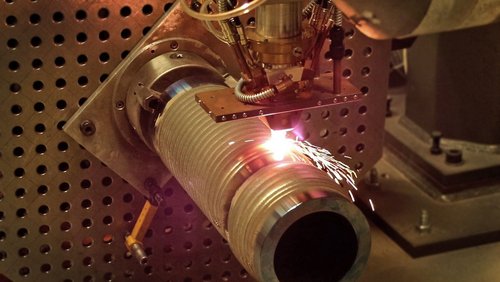
Top-Hat Profile
Here in particular, laser cladding has better traits. Short but intensive energy inputs that do not cause deformation are sufficient for melting. The energy input can also be fine-tuned while the process is running. The irradiation can thus be adapted very precisely to each component zone, from which highly sensitive, filigree components in particular can benefit. The best results in laser cladding are generally achieved with diode lasers.
The so-called top-hat profile of laser generates a uniform energy input and thus ensures uniform surface treatment. As a result, there is little mixing of coating and base material, making it possible to achieve particularly thin layers. In contrast, other laser types with a classic Gaussian beam can cause significantly greater mixing due to the high intensity at the center of the beam. The wavelength mix, typical of diode lasers, offers further advantages. It generates very calm and low-spatter melt pools and thus ensures high coating qualities. On top of that, the cost-effectiveness of the diode laser provides no room for criticism. And with an efficiency of up to 50 percent, it has the highest energy efficiency of all available industrial lasers.
Conclusion
The final result is that, depending on the preference, diode laser-based cladding can be used to achieve average to very thin coatings that are able to withstand even hard knocks and impacts, thanks to their high stability. On account of the motivation and coating material, such coatings can protect component surfaces from wear and corrosion and thus significantly increase their service lives. In addition to the initial coatings, the process can also be successfully used to repair worn surfaces or damaged components. Another important area of application is additive manufacturing, also known as 3D printing. Here, layers of identical or different materials are applied, layer by layer, to produce an entire array of components in almost any desired shape or structure.
Even this brief overview has made one thing crystal clear: Diode laser-based cladding opens up a wide range of processing options and can prove itself with high quality standards that many other processes cannot always meet. But what exactly do the three main applications of "coating, repairing and generating" look like? And where are they being used? The answers to these questions will be thrashed out in the next three parts of our series.
Learn more about Laser Cladding.