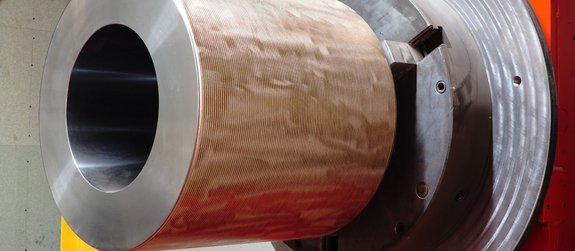
Laser Cladding Today: Status of Technology (Part II)
Machine blades and boiler walls, brake disks and gearbox bearings: the diversity of components coated with diode lasers is enormous. Diode laser-based coating processes today are almost as diverse as the treated components themselves. Part 2 of our series on laser cladding provides a brief overview.
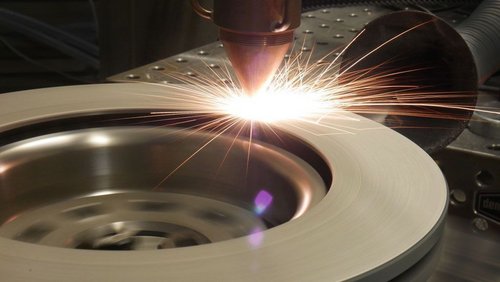
Cladding, Repairing, Generating
In the three part of laser buildup welding - cladding, repairing, generating - cladding is in a sense the keynote. It is used primarily in the production of new components (initial coating). The aim is almost always to create a protective effect and thus extend the lifetime of the treated components. Body and transmission components, oil and gas boilers, as well as pipe walls in power plants, are examples, that are protected from rust, aggressive chemical compounds or dangerously high temperatures by anti-corrosion coating. In the case of machine knives, axles, shafts or brake discs, which are exposed to strong bump and friction forces in daily use, special anti-wear protection increase their service life. In gearbox bearings, anti-friction coatings can prevent critical material friction during start-up and run-down phases, such as in the plain bearings of wind turbines.
Furthermore, coatings that increase the lifetime of components through a self-sharpening effect are also used in agricultural machinery knives, for example. In all these applications, the diode laser has now established itself as the most effective cladding tool. It has replaced competing technologies such as thermal spraying or plasma deposition welding. With its help, all classic coating materials such as tungsten carbides can be processed excellently and thus high-quality coatings of different thicknesses can be realized.
Nevertheless, the success of diode laser-based cladding is not based solely on the advantages of diode lasers described in Part 1 of our series. At least as important are the various processes that manufacturers such as Laserline have developed in collaboration with their technology partners to meet the needs of different components and their application profiles.Cladding is not just cladding here. What is perfect for cladding a car body sheet may be the wrong approach for knives, brake discs or gear wheels. In fact, coating processes are now almost as diverse as the components themselves. In many cases, no meaningful implementation is possible without process individualization. Anyhow certain basic features can be defined that are repeated for comparable components.
The coating process of flat components turns out to be the least complicated. Classic metal sheets can usually be cladded with a wide beam in repeated lanes and thus quickly and effectively. For large components, special high-volume processes have been developed in which diode lasers can fully exploit their performance advantages. With 11 to 20 kW laser power and around 90 percent powder efficiency, previously unattained powder application rates of up to 14 kg/h can now be achieved. Tests with a 50 kW laser power even achieve powder coating rates of around 35 kg/h and area rates of around 3.5 m²/h - compared to standard processes, a threefold increase in cladding performance.
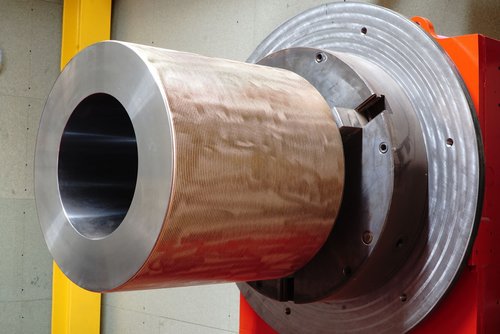
Use of round spots
However, even with flat components of varying thickness, the implementation is no longer quite so simple. In the case of machine knives, for example, which taper towards the blade, wide beam treatment would prevent the necessary heat dissipation into the thicker areas of the component. This in turn would lead to deformation or melting in the blade area. In order to avoid such damage, more precise, energetically well-dosed irradiations with the classic round spot which are precisely tailored to the respective component design, must be realized. The same procedure applies to components with complex surface geometries, such as plain bearings or gear wheels. The wide beam cannot be used effectively here either. Instead, point-precised and individualized coatings using round spots should be considered.
Even with rotationally symmetrical components such as gearbox axles or metal tubes, rapid traversing with the wide beam turns out to be problematic since processing optics with coating nozzle usually cannot be rotated around the workpiece. A rotation of the optics is basically conceivable, but considering the gravitational forces it would make a uniform powder application impossible. Special high-speed variants were therefore developed as an alternative. Here, the process optics are fixed, and the component is moved vertically around its longitudinal axis on a lathe. This process operates at very high speeds. Regarding to this, high area rates can be achieved in a short time. Due to the extremely short exposure time, very thin coatings can be produced. The same approach is used for wear protection coatings for brake discs, except that a horizontal direction of rotation is implemented here.
Conclusion
Of course, these examples can only hint at the diversity of cladding with diode lasers and the possibilities available to users. A detailed description of this matter would fill up many books. Nevertheless, even these small examples make it clear why diode lasers have become an indispensable part of industrial cladding: They have simply proven to be a universal tool. It is therefore no coincidence that new applications have already been targeted, such as copper coatings, which can be realized in a very energy- and material-efficient way with blue diode lasers. But before we report on this, we will first continue with our current series on laser cladding. The next part will be dedicated to repair welding shortly - stay tuned!
Learn more about Laser Cladding.