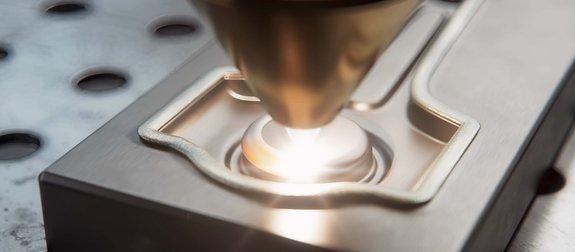
Laser Cladding Today: Status of Technology (Part III)
In the trinity of the major areas of laser buildup welding applications, so-called repair cladding occupies a middle position. It has similarities with both cladding and additive manufacturing, but ultimately represents a process world of its own. Today, in the third part of our series on the different variants of laser buildup welding, we reveal which repair procedures are carried out there and how.
Part 3: Repair Cladding
Rollers, gears, drive shafts, tools - sooner or later, metal components that are subjected to heavy loads almost always contain cracks or damaged surfaces and are thus no longer fully operational. However, the end of their lifetime has not necessarily been reached. Instead of replacing the component with a new one, in many cases the more economical as well as faster solution is to aim for repair. The keyword here is repair cladding: cracks or damaged protective layers are being closed or renewed, broken-off parts are being restored, and the component finally regains its full functionality.
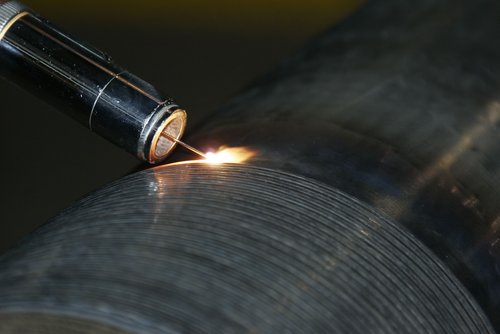
Common Methods
In the past, conventional welding processes, which are mostly hand-guided or only partially automated, were common methods for such repair coatings. In these cladding technologies, a metal wire or powder is usually melted onto the workpiece surface using an electric arc, creating the intended repair or protective layer. The disadvantages of these processes are the high heat input: it often causes severe component distortion and a large dilution with the base material, making the process unsuitable for filigree components in particular. Diode laser-based repair cladding is therefore increasingly being used as an alternative. It requires only moderate heat input, produces pore-free coatings and enables fast, efficient and simple repairs, even for filigree components. Here, a range of economical repairs smaller than one millimeter up to large components with repairs of several square meters can be covered, depending on the requirements and the component.
Fundamentally, the laser-based repair process differs slightly from the cladding one (initial coating) and is equally suitable for renewing damaged coatings as well as for closing cracks and repairing defective or faulty molds. For coating repairs, the worn defective material volume is first removed, the surface of the workpiece cleaned and the contour mechanically prepared. The coating material - wire or powder - can then be applied to the component. For this purpose, it is added to the local melt pool on the workpiece surface and melted along with it. In contrast to the application of wear or corrosion protection, however, materials identical to the base material or harder metal are usually used. The result is a new hard-wearing coating that is metallurgically bonded to the component. The thickness of the applied coating can vary depending on the application.
A typical example of such repair coatings can be found in transmission technology: In the past, drive shafts were often provided with a special wear protection coating made of ceramic, which sooner or later showed damage or flaked off. This damage used to be irreparable, which then also meant the end of the shaft's lifetime. Diode laser-based repair cladding has fundamentally changed this situation. After removal of the old ceramic layer, a new wear protection coating is now applied using stainless steel heating wire. This protective coating is far more durable than a ceramic coating and incurs only a quarter of the cost - a very significant advantage in terms of overall cost.
Other prominent examples of economical repairs include molds and tools used in primary forming and casting technology, as well as bearing seats, crankshafts, piston ring grooves, turbine blades and many others.
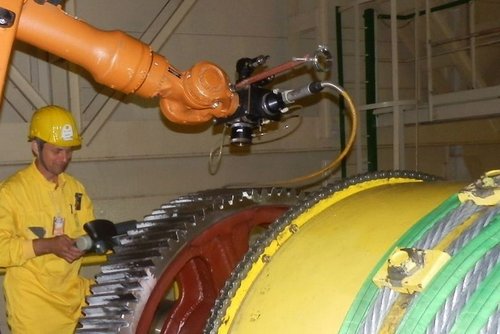
Repair of Cracks
The repair of cracks or worn out areas basically follows the same pattern - except that here cracks and damaged contours are filled or removed again layer by layer. Thanks to lightweight, compact mobile lasers that are even suitable for use on narrow scaffolds at high altitudes, this process can even be implemented in places that are difficult to access, such as fixed large gear wheels. In all these processes, laser-based repair cladding scores with a near-net-shape restoration of the component geometry and a lower heat input. In addition to that, there is a correspondingly lower thermal load on the component, which hardly causes any distortion. This means that even particularly sensitive components can be processed without any problems. Rework is kept to a minimum.
Conclusion
Relying on diode laser technology for repair cladding pays off in terms of effectiveness and economy as well as quality aspects. The efficiently simple repair of coatings is just as feasible as the closing of cracks or the restoration of broken contours. In this last point, however, repair cladding already overlaps with the third major area of laser buildup welding application: additive manufacturing, often referred to as 3D printing. We will turn our attention to this forward-looking process in the fourth and final part of our series.
Learn more about repair welding.