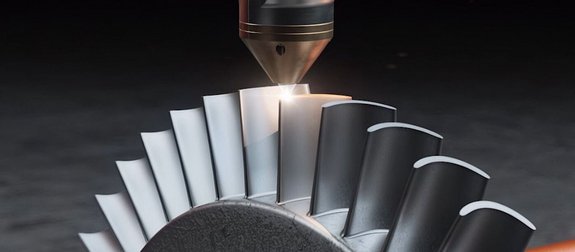
Laser Cladding Today: Additive Manufacturing (Part IV)
Laser buildup welding is nowadays represented in numerous industrial manufacturing areas. This also includes the manufacturing of complex components using the layering principle - also known as additive manufacturing or 3D printing. The last part of our series is now dedicated to this area of application.
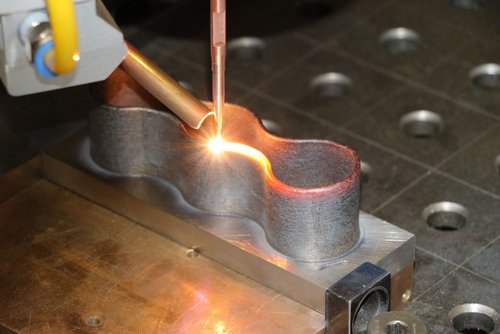
Part 4: Additive Manufacturing
The importance of additive manufacturing - often referred to as 3D printing - has increased significantly in recent years, and for good reason. This is because both forming techniques and subtractive manufacturing methods, in which components are generated by machining processes, are not well suited for the production of complex, individual components due to a lack of design flexibility in the manufacturing process - in addition, there is often significant material loss. Conversely, additive manufacturing processes enable simple realization of three-dimensional components with complex geometries thanks to the technology of layer-by-layer construction. These processes are particularly suitable in cases where a high level of individualization is required. Furthermore, far less material is lost here than during a machining process.
Among the competing additive manufacturing processes, the comparatively recent laser-based method has gained increasingly attention in the industrial environment lately. Although it was developed for the rapid creation of one or more prototypes, the generative manufacturing method using lasers has long since been used to produce full-scale molds and small series. Moreover, the process has also found its way into repair welding – whether it be in the repair of break-offs or for the restoration of surface structures. Additive manufacturing with diode lasers, which is based on classic buildup welding, has proved highly successful, whereas the LPBF (Laser Powder Bed Fusion) process - in which the component is generated by selective beam melting in a powder bed - has so far proved too slow and costly. The biggest non-laser-based processes competitor is currently WAAM (Wire Arc Additive Manufacturing) - a wire-based process that uses an electric arc to melt the layer material and surface. However, the large heat input, which sometimes causes severe distortion, as well as the poor final contour accuracy and unsteady melt pool guidance with strong spatter formation proves to be a disadvantage here.
Although the diode laser-based process (in which three-dimensional shapes are realized) is also comparable to buildup welding, the process setup is quite different. Work is carried out with a system consisting of a laser, a flexible 3D print head and a metal powder nozzle or wire feeder. During the process, the print head moves across the working platform referred to the three-dimensional design plan and melts the workpiece surface and layer material. The coating material used for the application is stainless steel as well as metals such as aluminum and titanium but also superalloys such as those used in aircraft construction. During the manufacturing process, it is also possible to switch between different materials. This means that different requirements, such as wear resistance, thermal conductivity and ductility, can be combined in one component by selecting materials, which cannot be merged by a homogeneous material alone. After solidification and cooling of the applied material, the process continues with the next layer. The component is in thus built up layer by layer. Shapes and structures are ultimately realized in a continuous process - and with almost no material loss, reworking or tool wear. The top-hat profile of the diode laser also ensures even melt pools, smooth process control and homogeneous, crack-free material layers.
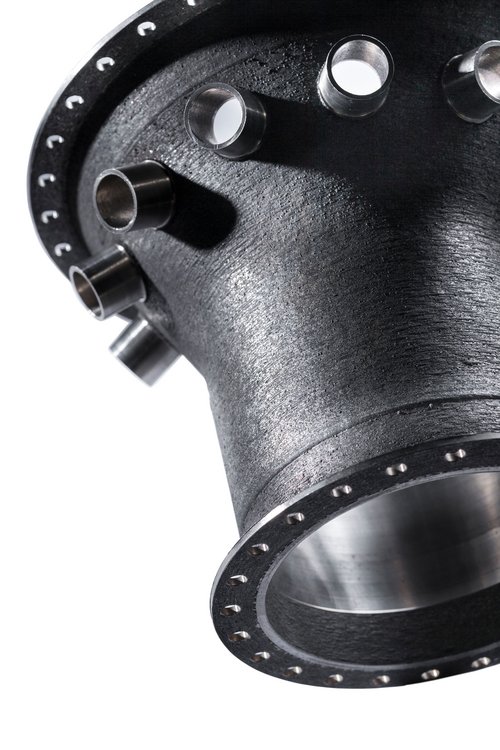
The Advantages
The advantages over the competing applications quickly become clear: Compared to the LPBF method, more than 10 times larger buildup rates are achieved and thus a significantly shorter process time. In comparison with the WAAM method, on the other hand, the diode laser-based method scores with steady, low-spatter melt pools as well as a lower energy input, which enables component distortion to be minimized. To optimize the production process, it is also possible to integrate the laser beam source into machine tools. In milling machines, for example, an alternation of additive powder application and subtractive machining can be realized in this way: The laser is therefore responsible for the powder application, whereas the milling head realizes the machining finishing. When used in twelve-axis milling machines, the application possibilities of the beam source expand even further: In addition to powder application, it can also be used for welding and hardening – assumed that appropriate optics are used.
Conclusion
It is therefore no wonder that laser-based additive manufacturing is increasingly in demand: Even components with complex, individual geometries can be realized with little material loss and almost without reworking - in addition, the finished workpieces are convincing due to being crack free and overall its very high material quality. To sum it up, additive manufacturing with diode lasers is also convincing in areas where it was not expected before. This brings us to the end of our series, but not to the end of laser buildup welding. Despite all its successes, its future has only just begun.
Learn more about additive manufacturing.