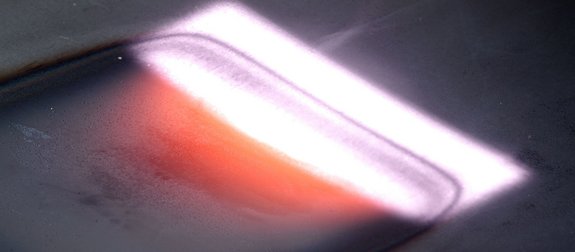
Softening of high-strength steels with diode lasers
Technically superior but economically untenable — until now, this was the destiny of diode lasers when it came to softening high-strength steels. However, thanks to a technological innovation by Fraunhofer ILT, their use will become economical soon.
Still, there’s no reason to be biased. Softening high-strength steels via laser heat treatment seemed at first doom to fail, not technically but economically because the feed rate at laser beaming was simply too low. With the vital process parameters — a homogeneous heat distribution in the steel and a small temperature gradient — achieving more than a meter per minute was not possible. This was not very convincing given that the industry required three to ten times as much. And this despite the fact that the lasers seemed quite suitable, especially diode lasers which had proven themselves very well in prototypes and research projects. The flexible and precise material processing, the huge focal spot size, the homogeneous intensity distribution — all these allowed for optimal heating of the work piece zones and provided excellent softening results, except that the process was too slow. It didn’t even help that diode lasers excel in high electrical efficiency levels. Other technologies like induction, infrared rays or gas flames made higher process speeds possible. Those who wanted to prepare or generate forming processes or crumple zones were better off keeping away from lasers.
But as mentioned before, we should not be biased. And that is because laser heat treatment is only uneconomical when you treat the workpiece only on one side. For when the laser beam is used on two sides, the distance of the heat flow is halved. Homogeneous heat distributions and low temperature gradients can now be realized within a clearly reduced time. This simple but ingenious conclusion had the Fraunhofer Institute for Laser Technology (ILT) in Aachen, Germany. The idea was realized using Laserline’s diode lasers and special processing optics which were decisively advantageous for this process: the user can combine fix spot widths with big, flexibly designable spot lengths, and can thus gain optimal surface effect. This was made possible by zoom homogenizers with bidirectional homogenization and spot lengths of up to 80 mm. With these Laserline-developed optics, focal surfaces with different measures and geometries can be created and dynamically modified during the running process. It does not matter whether it is line spots, square or rectangular spot geometries, everything is possible. Furthermore, a pyrometer was integrated into the optics to monitor the temperature and control the radiation.
Equipped in such a way, the Fraunhofer engineers dared to put it to trial. Two of the mobile Laserline diode lasers of the types LDF 12000-100 (12 kW) and LDF 16000-100 (16 kW) were brought to the test facility and the new idea was tested. It proved itself immediately. At serial softening of high-strength steels with merchantable yield points of 1200 or 1500 MPa at a spot size of 5 x 25 mm², continuous feed rates of 15 meters per minute could be reached.
With such values, the industrial capability of laser-based softening is no longer questioned. And opportunities are yet to be exhausted. At first, the possible maximal spot size is yet to be used; secondly, Laserline’s diode lasers are also available in higher power-classes. At the Laser World of Photonics 2017 in Munich, for example, a diode laser system with 60 kW output power was presented. With such systems, feed rates of up to 20 meters per minute have become imaginable. Mostly likely, you might already know this from laser cutting.
Currently, Fraunhofer ILT is conducting some final test series. In those tests, they experiment with different intensity distributions within the diode laser spot to further optimize the heat transfer. As soon as these test series are completed — which could be any time now — the new process can be used in serial softening under real conditions.
What have we learnt from this? There are always two sides to the same coin, and sometimes you simply have to radiate things from both these sides.